Fangs "new" toy!!
I think you are lucky it snapped the allen key, I bet it would have snapped that whole casting off with any more pressure.
GOVERNMENT WARNING!:
If you are having individual free thoughts please switch on your TV immediately and watch x factor, or go shopping, or buy a happy meal, free thought will lead to extremism.
If you are having individual free thoughts please switch on your TV immediately and watch x factor, or go shopping, or buy a happy meal, free thought will lead to extremism.
Right then, thought I'd better update a bit more.
Yesterday I decided to drain the oil from the beast before I put it on the work bench.
While this was going on I gave the engine frame and brackets a quick once over with spray.
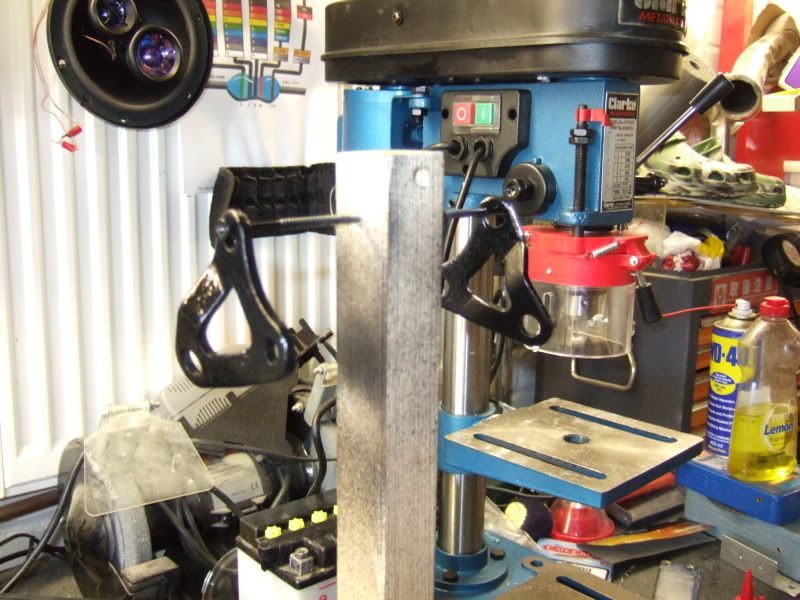
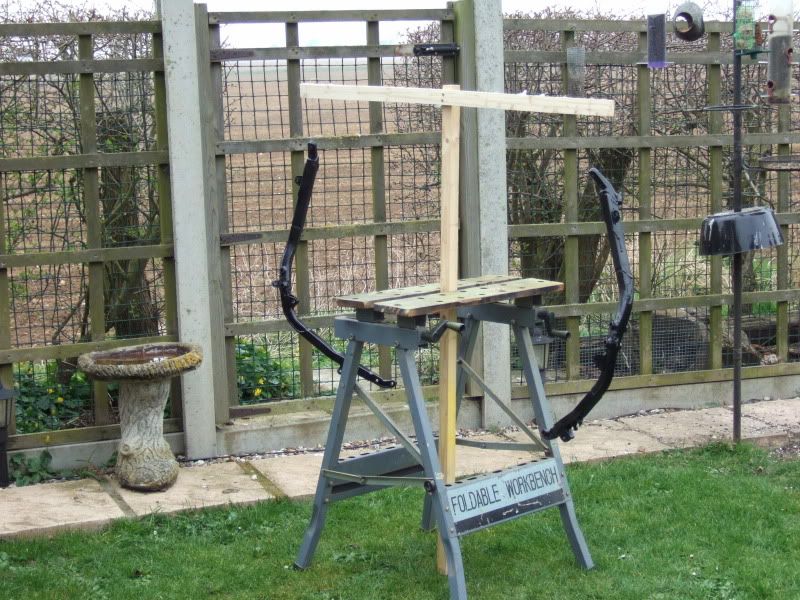
And gave the exup valve a quick shuftty, as its been sat for 2 years since I did it last.
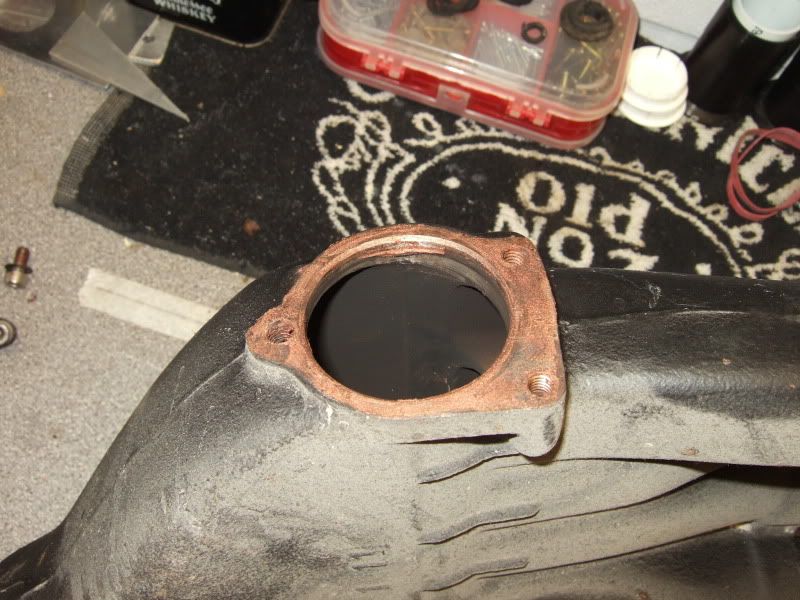
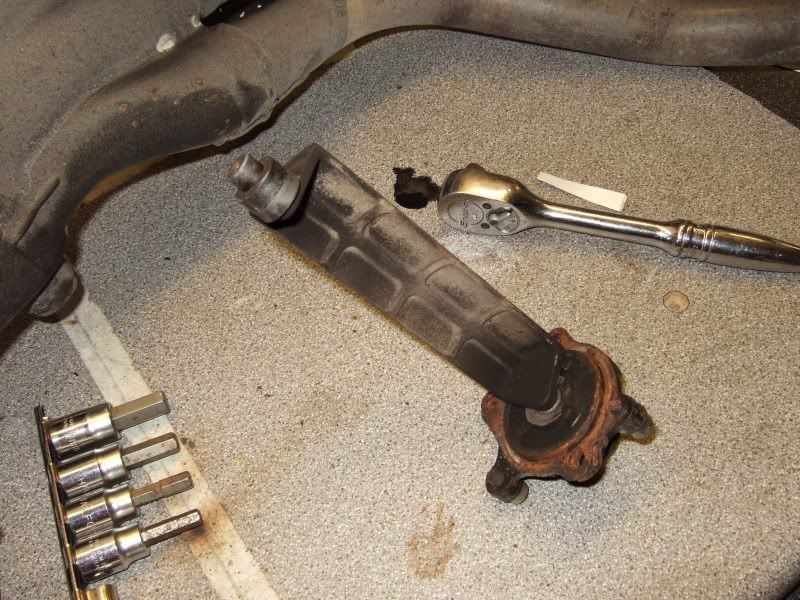
Then with a little help got her on the workbench ready to check the valves
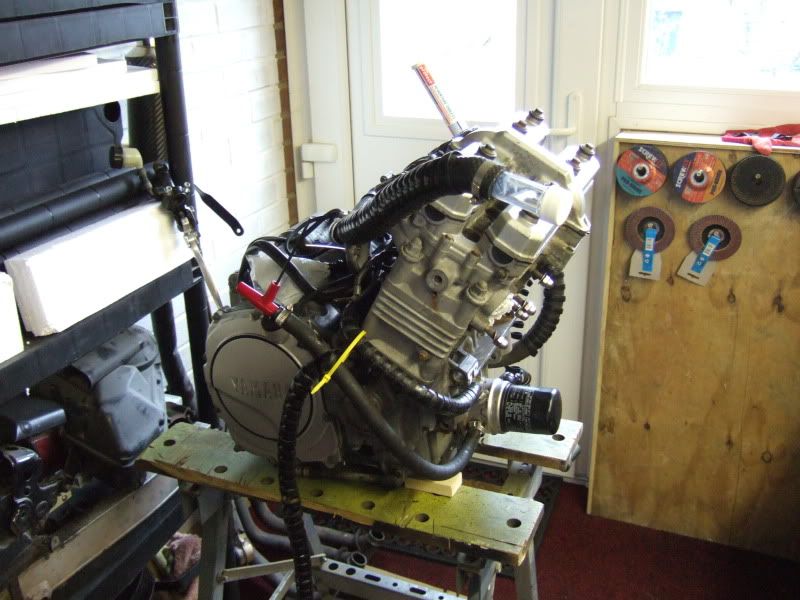
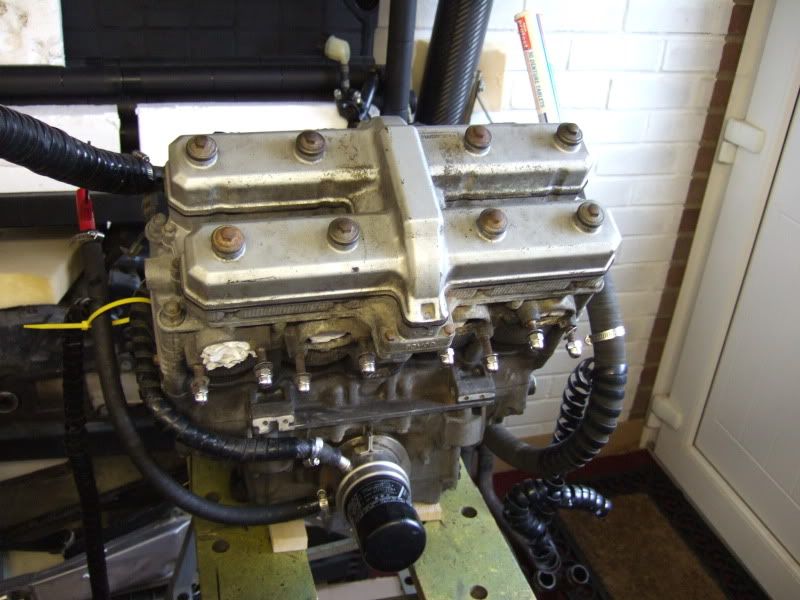
So today I go out and check the valve clearances
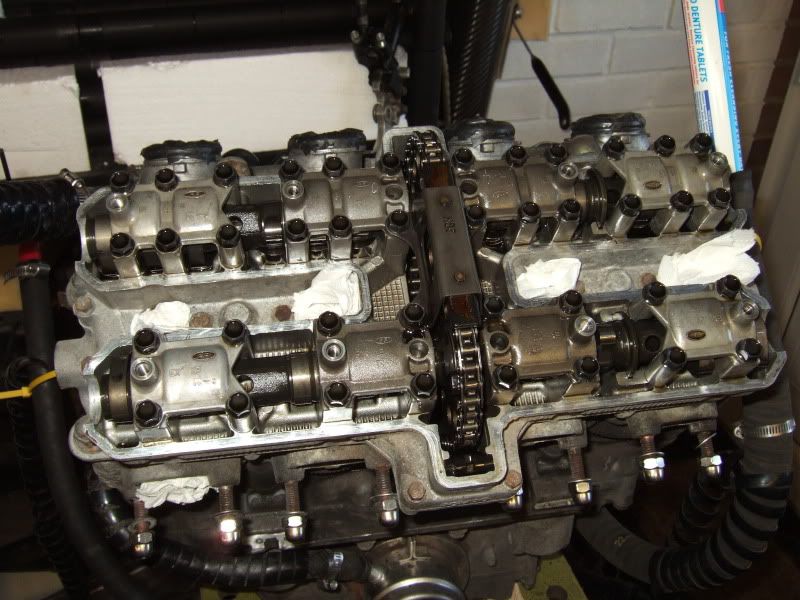
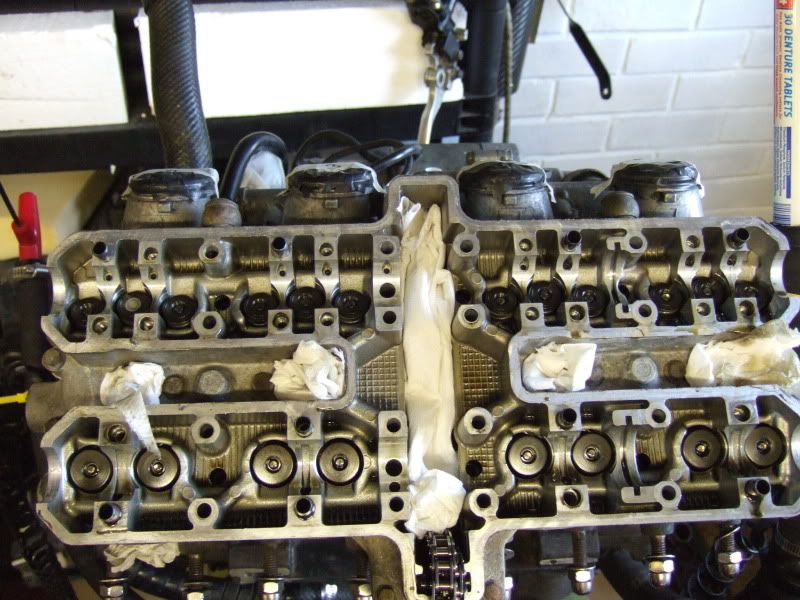
All good, apart from a small hiccup, looks pretty good inside and has even had a new camchain fitted at some point.
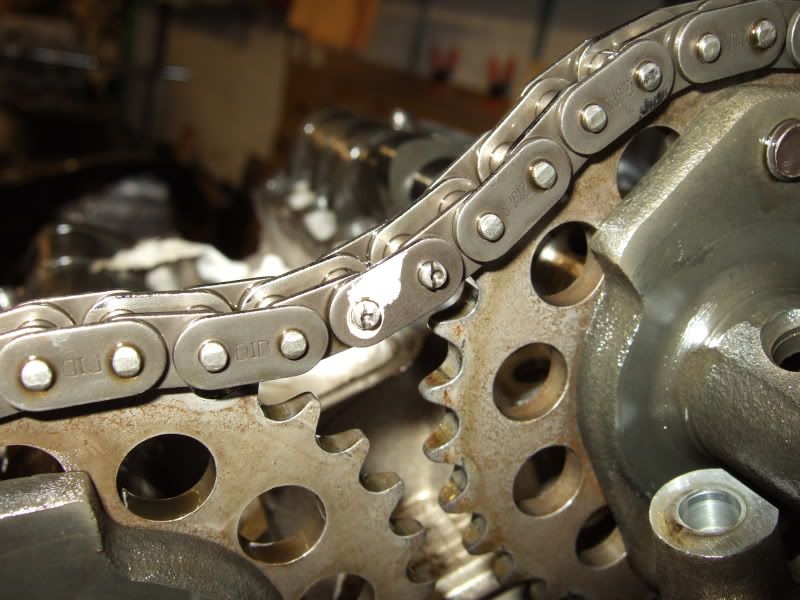
So tomorrow, I'll whip her onto her back and remove the sump to see what its like in there.
And also see if I can source a later model sump pan as this one seems to be from an earlier model that had an oil cooler, as where the oil cooler feed and return pipes connect there is a makeshift pipe around the back of the sump connecting one to the other.
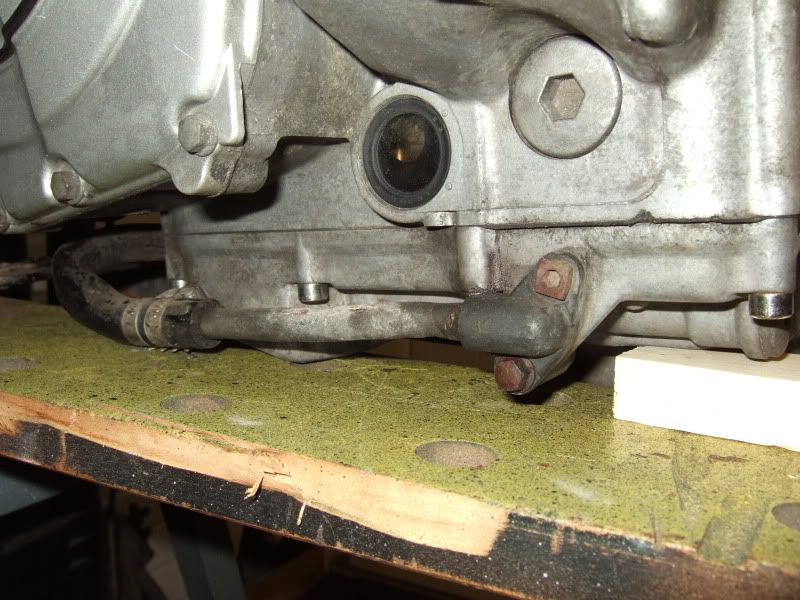
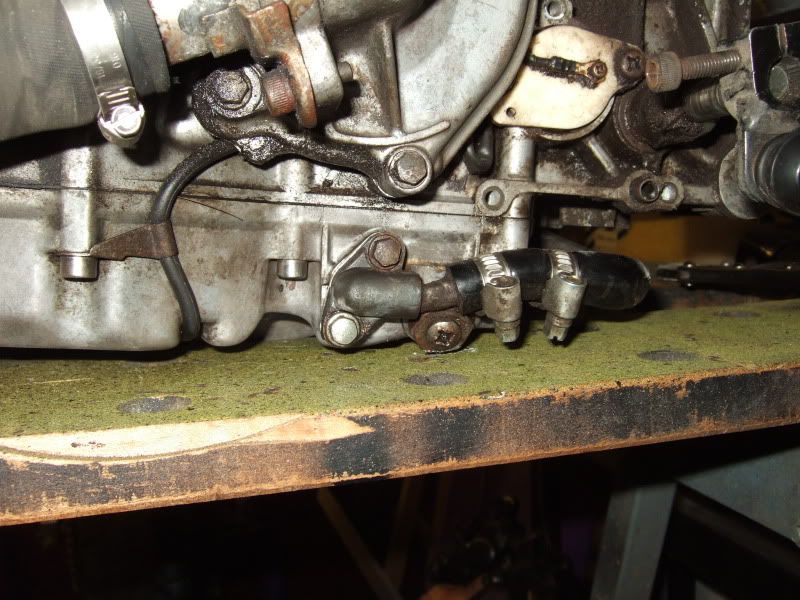
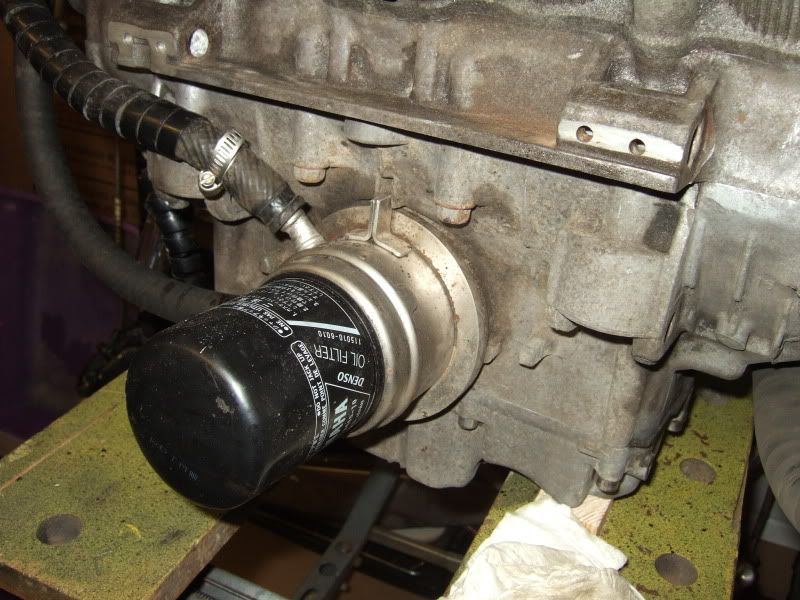
I will glean what information I can on this in the workshop section
Yesterday I decided to drain the oil from the beast before I put it on the work bench.
While this was going on I gave the engine frame and brackets a quick once over with spray.
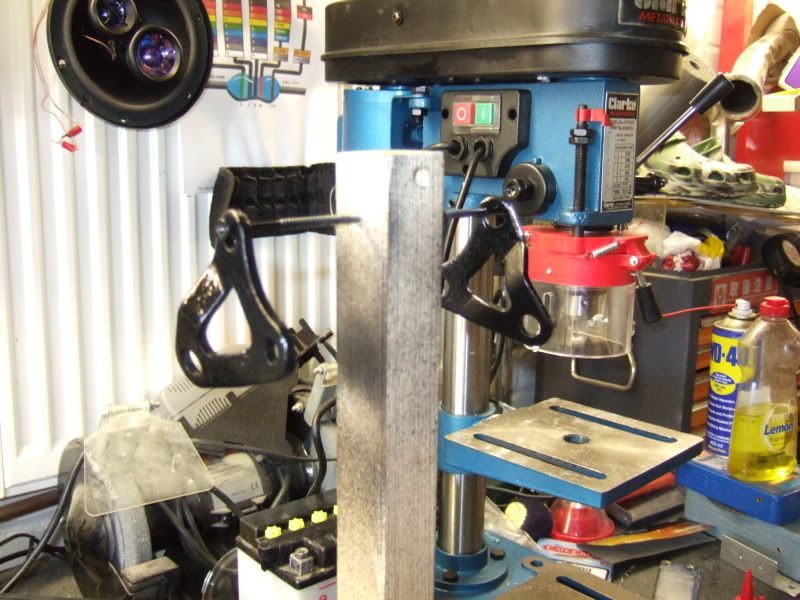
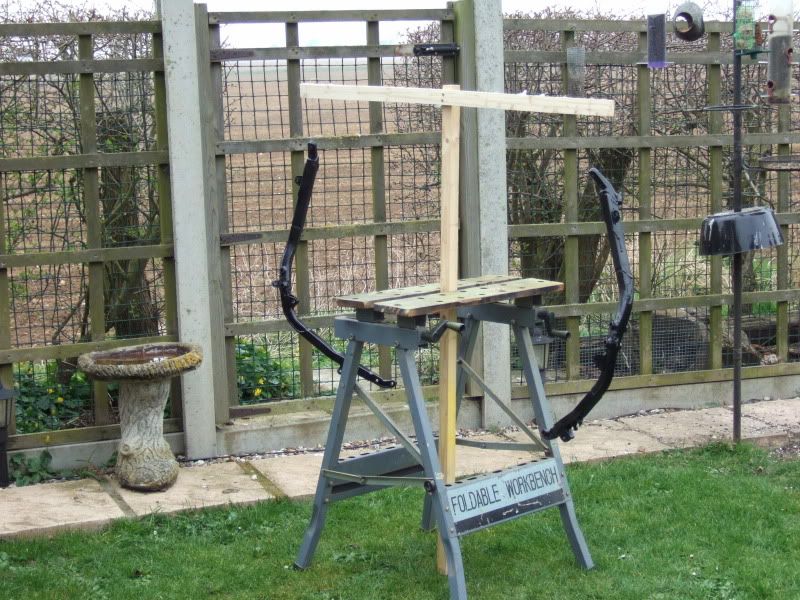
And gave the exup valve a quick shuftty, as its been sat for 2 years since I did it last.
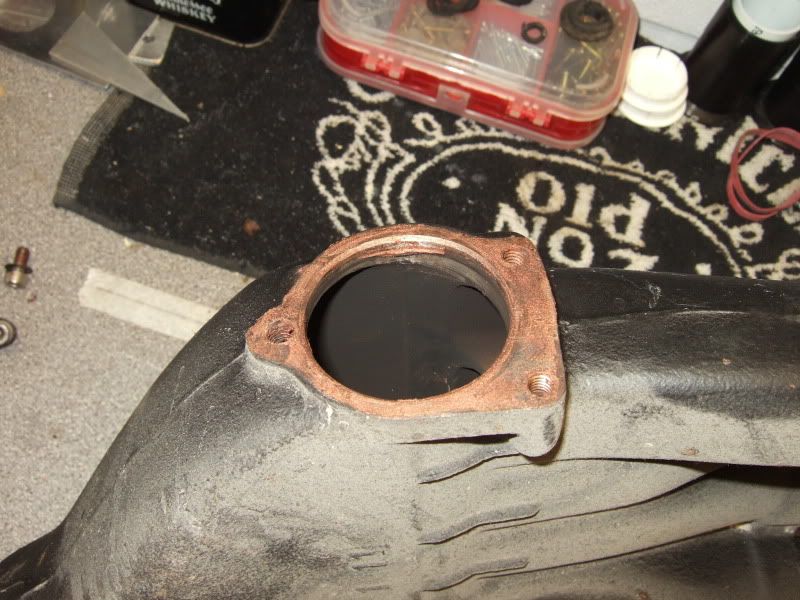
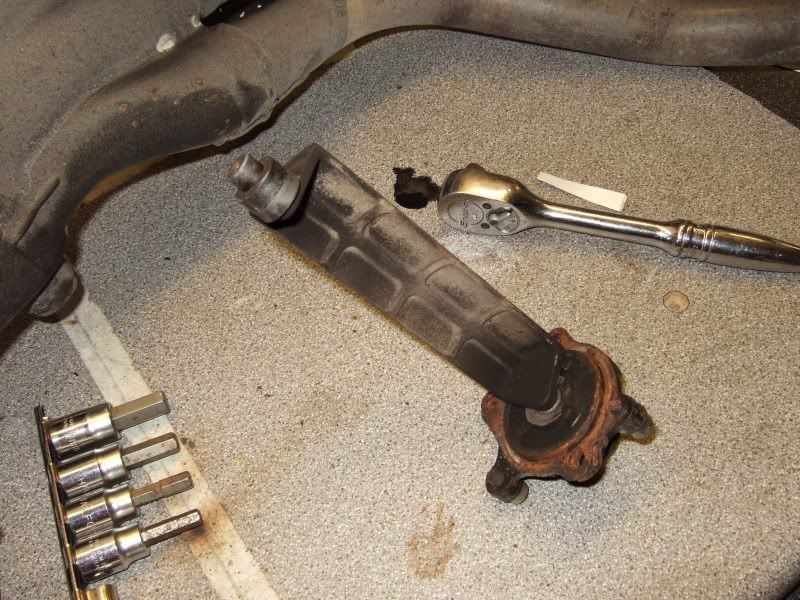
Then with a little help got her on the workbench ready to check the valves
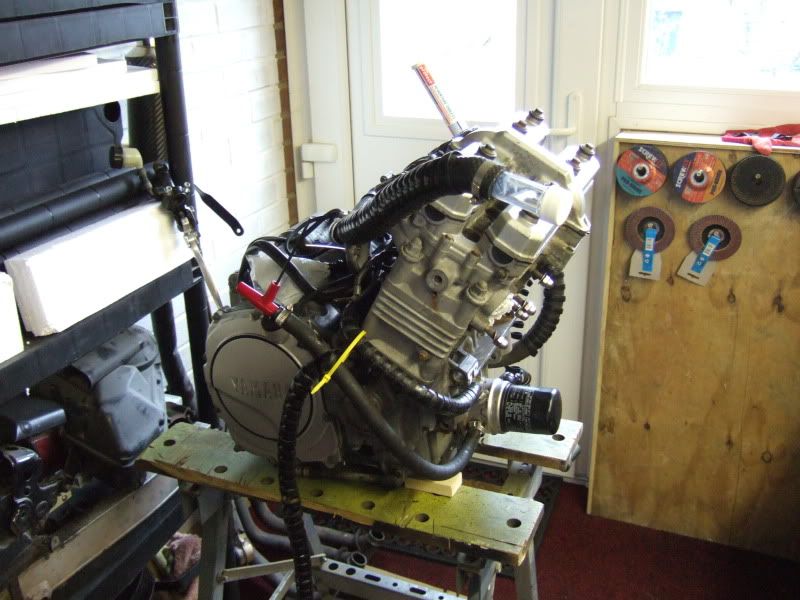
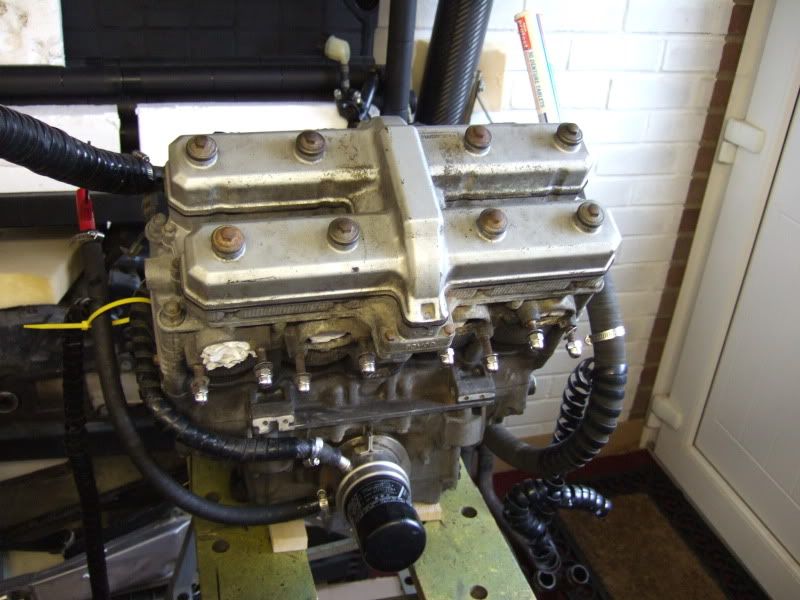
So today I go out and check the valve clearances
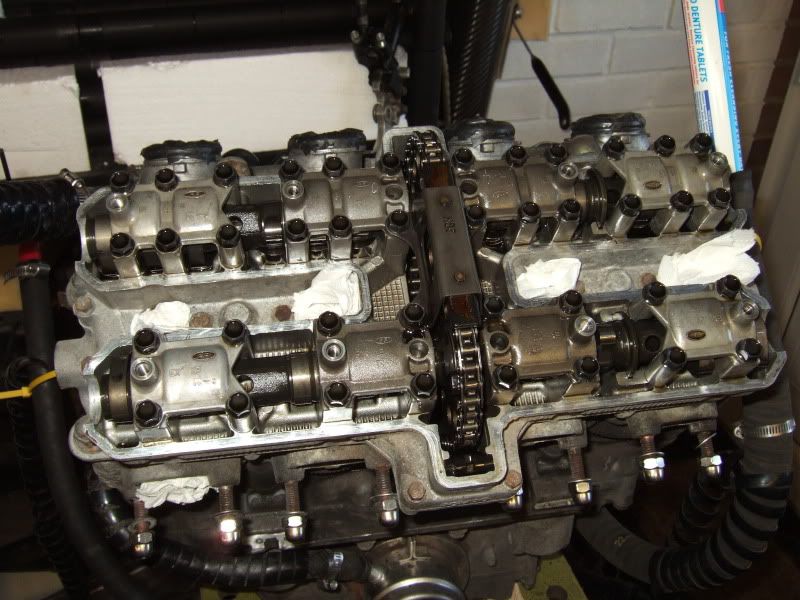
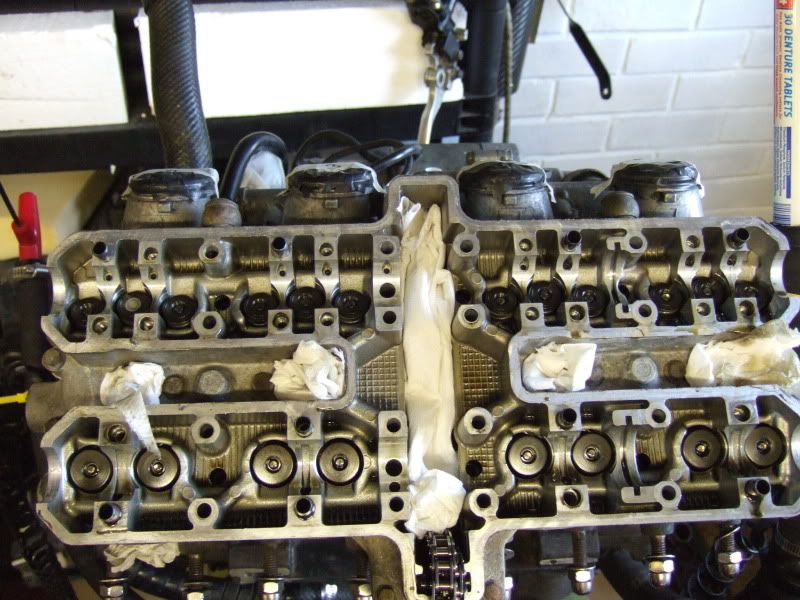
All good, apart from a small hiccup, looks pretty good inside and has even had a new camchain fitted at some point.
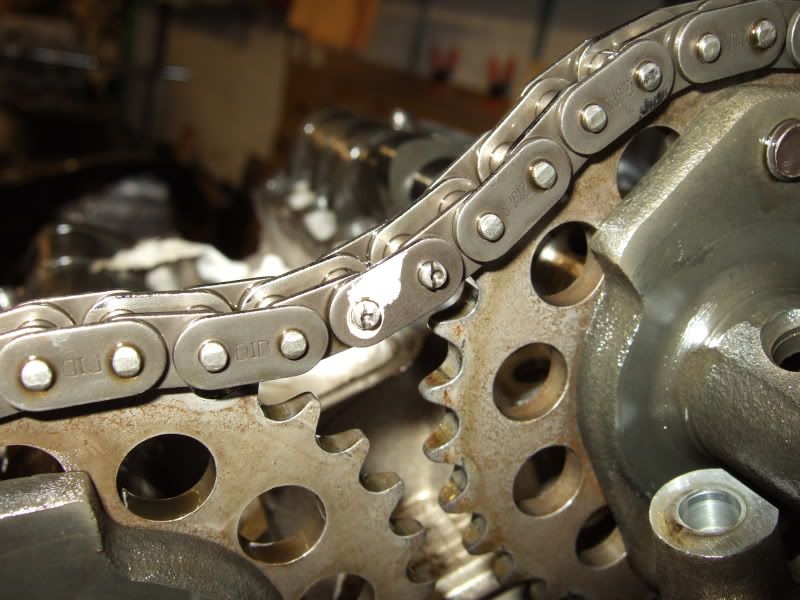
So tomorrow, I'll whip her onto her back and remove the sump to see what its like in there.
And also see if I can source a later model sump pan as this one seems to be from an earlier model that had an oil cooler, as where the oil cooler feed and return pipes connect there is a makeshift pipe around the back of the sump connecting one to the other.
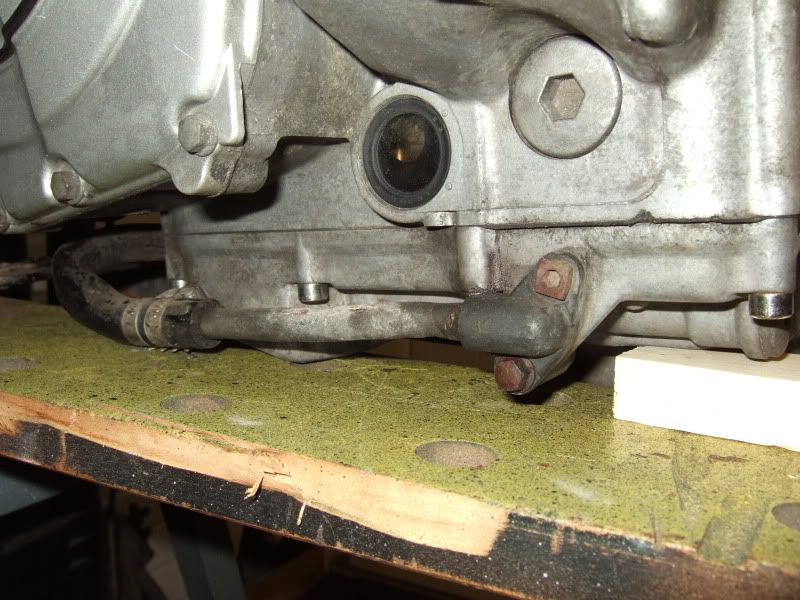
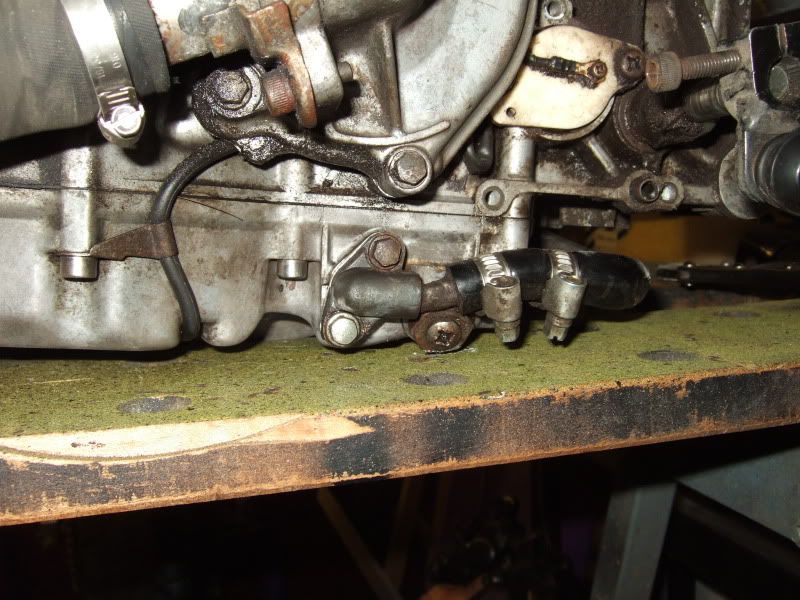
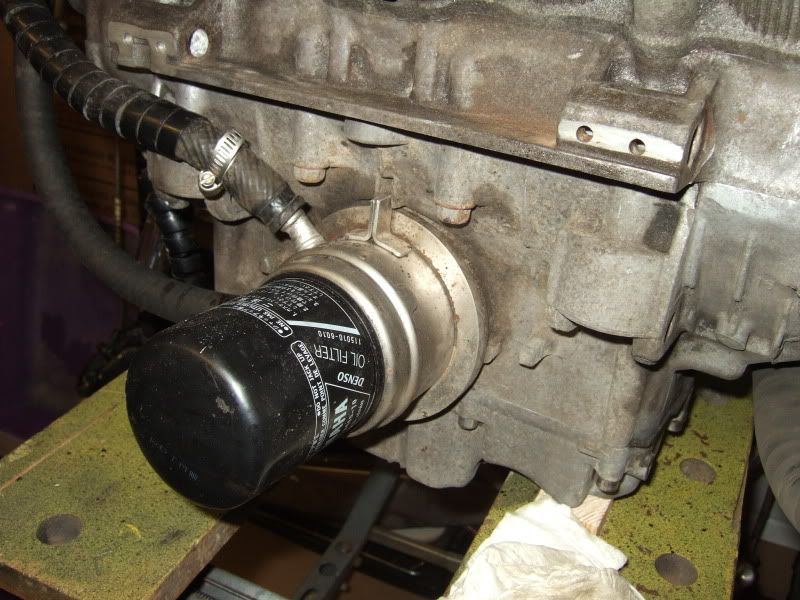
I will glean what information I can on this in the workshop section

Never Ever Bloody Anything Ever!!!
Just been reading this episode & came across this quote...as far as i'm concerned if it helps just one person a trip to the bike shop to have something simple done, then it's been worthwhile.fang wrote:Forgot to add that full credit for the tool should go to Yamaexup as he got there firstStig wrote:: oh and i've saved the images of the fork tool to use in the update i'm still doing...if thats OK with you. Pictures are always better than words in this instance![]()
![]()
![]()
http://www.exup1000.co.uk/phpBB2/viewtopic.php?t=9811
dont want to be sued for copyright infringement
otherwise I'll not be able to afford to finish the project
Keep up the good work Fang...I also have an assistant who is asked to help out in the shed from time to time when I need another pair of hands. I'm looking forward to the next installment already.
Not much to report, but thought I'd better update otherwise you lot will think I've dissapeared for another year!!
Got home from work yesterday and only had an hour so cleaned and sprayed cam cover as it was a bit tatty, and also sprayed frame rails with gloss black, as I only had satin black the other day.
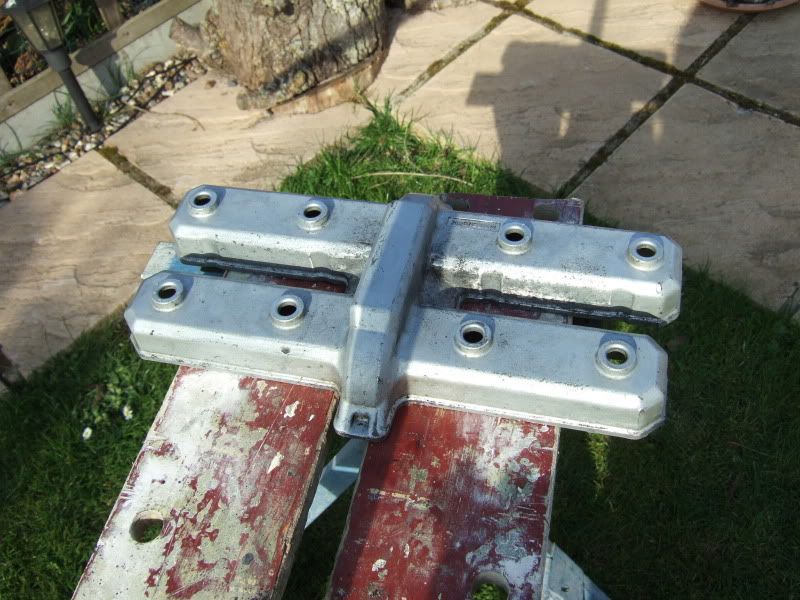
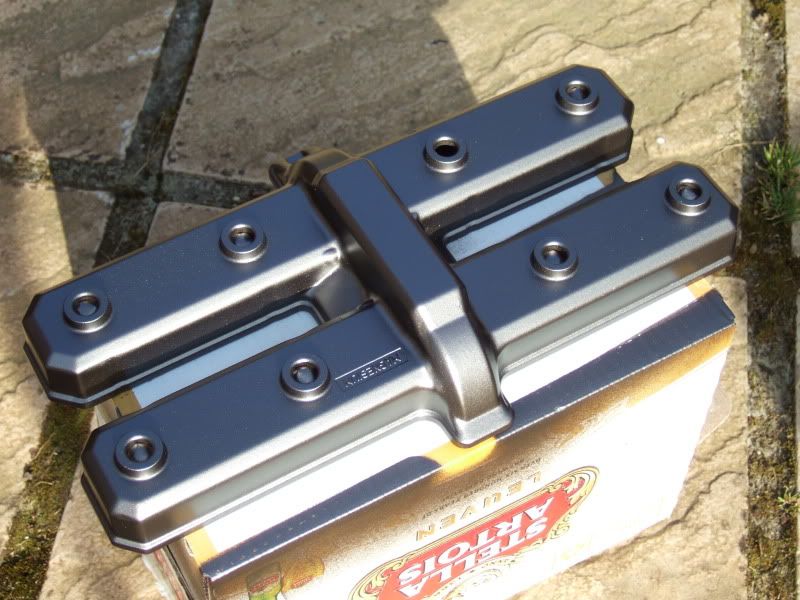
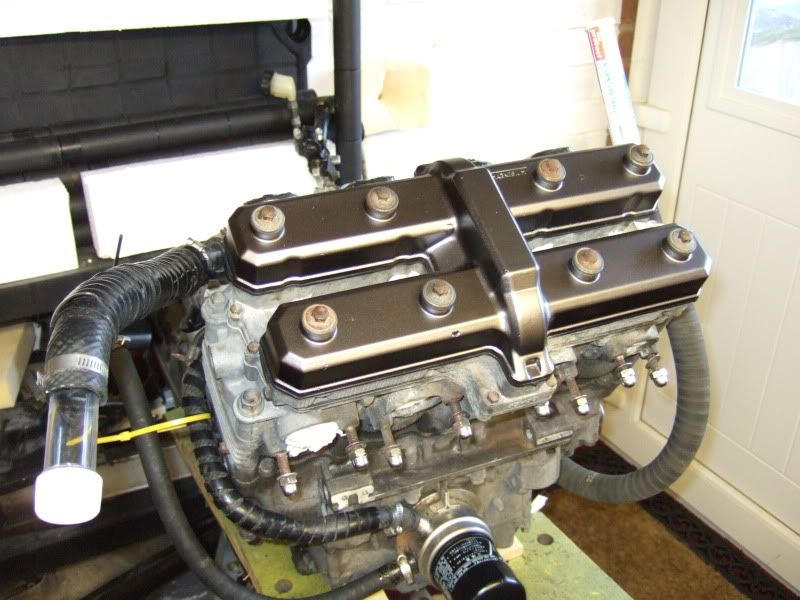
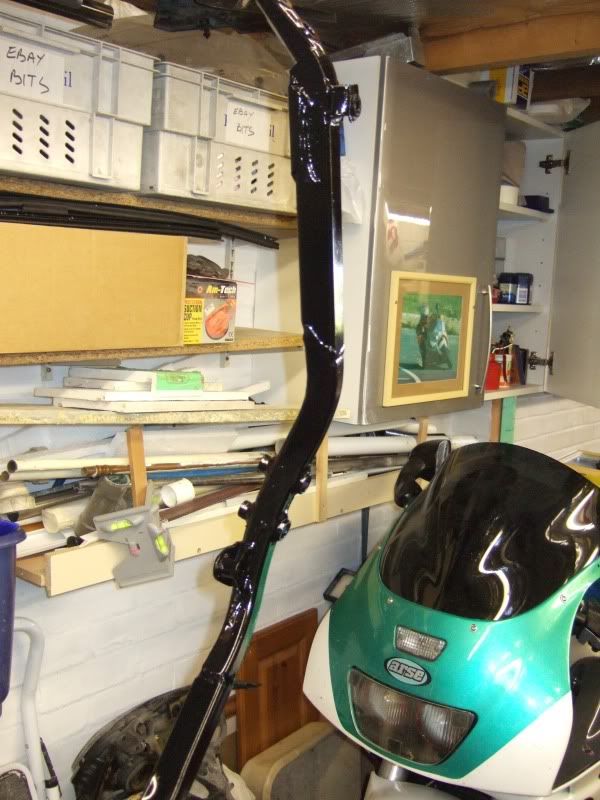

Got home from work yesterday and only had an hour so cleaned and sprayed cam cover as it was a bit tatty, and also sprayed frame rails with gloss black, as I only had satin black the other day.
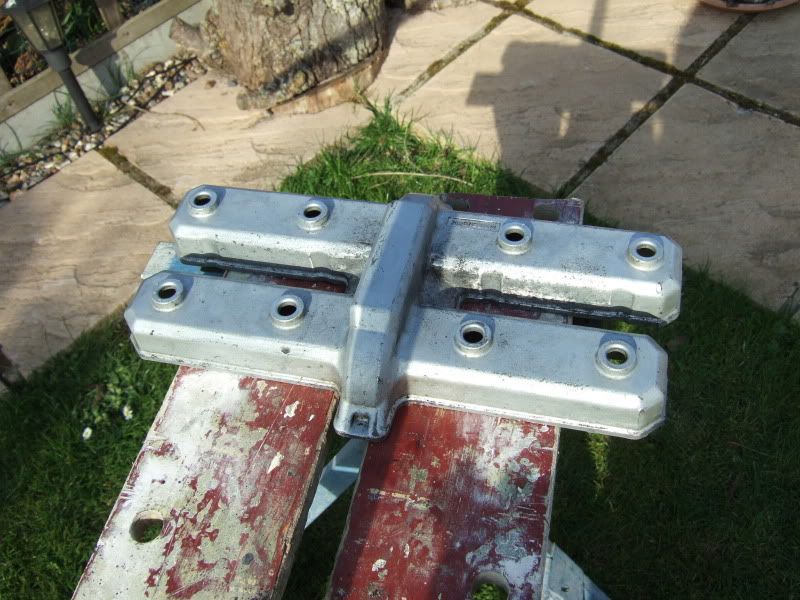
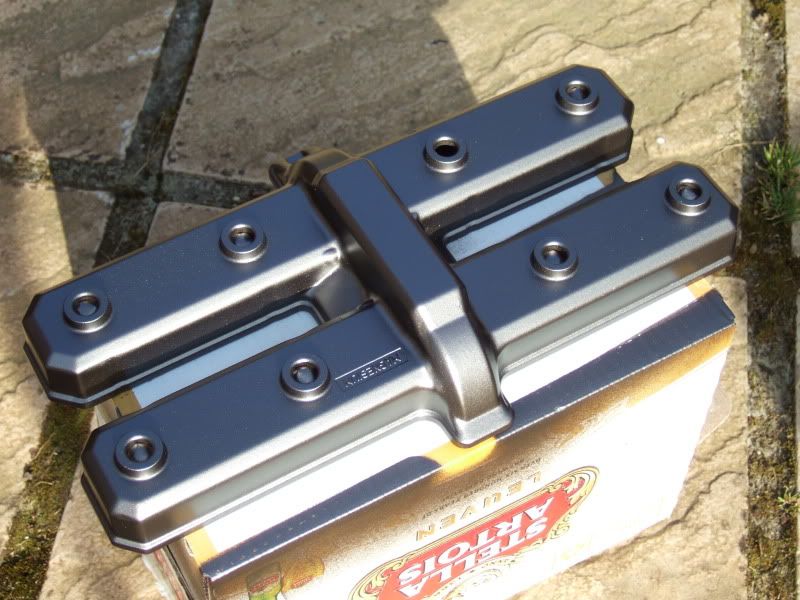
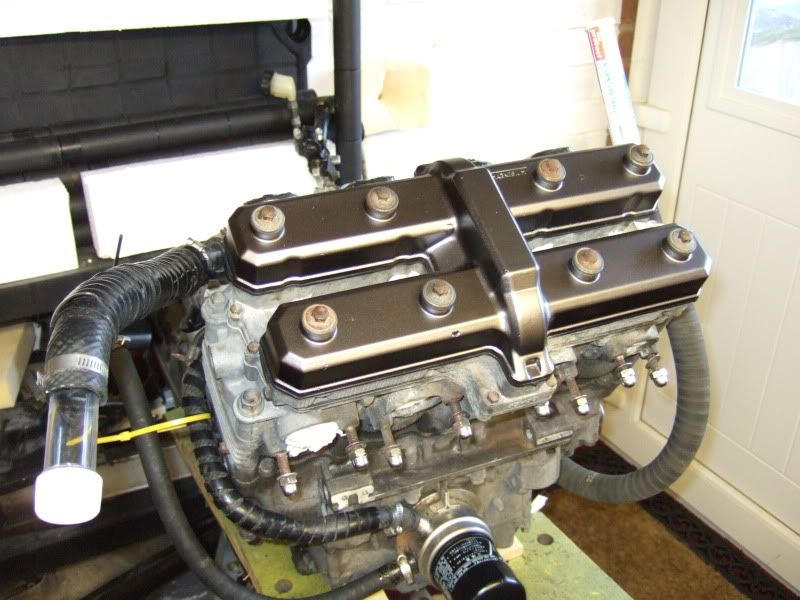
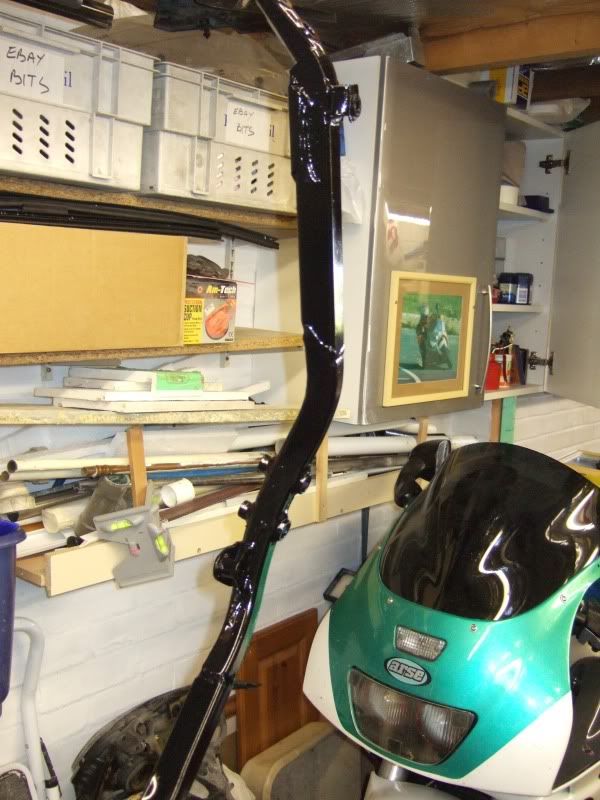
Never Ever Bloody Anything Ever!!!
Little more done this afternoon.
Rolled the engine onto its back so I could take the sump off and check all was well and to also try and figure out what to do about the oil cooler bypass arrangement.
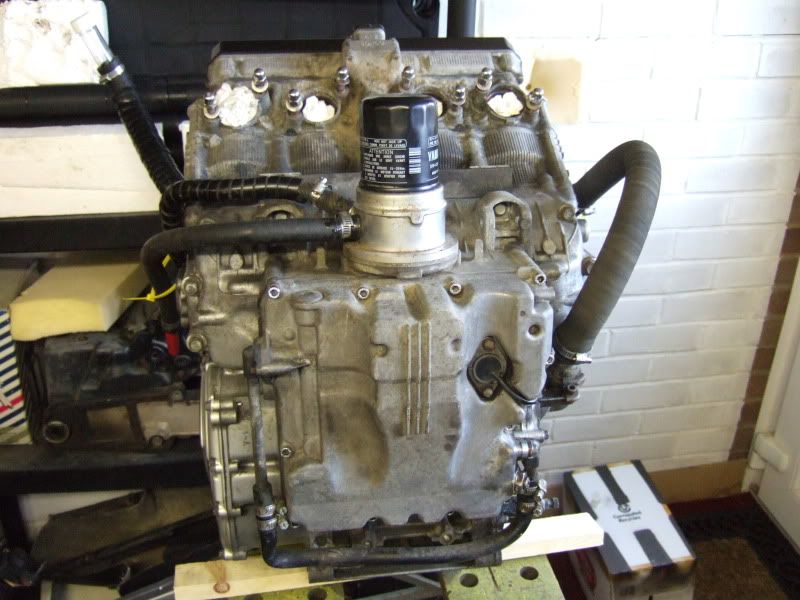
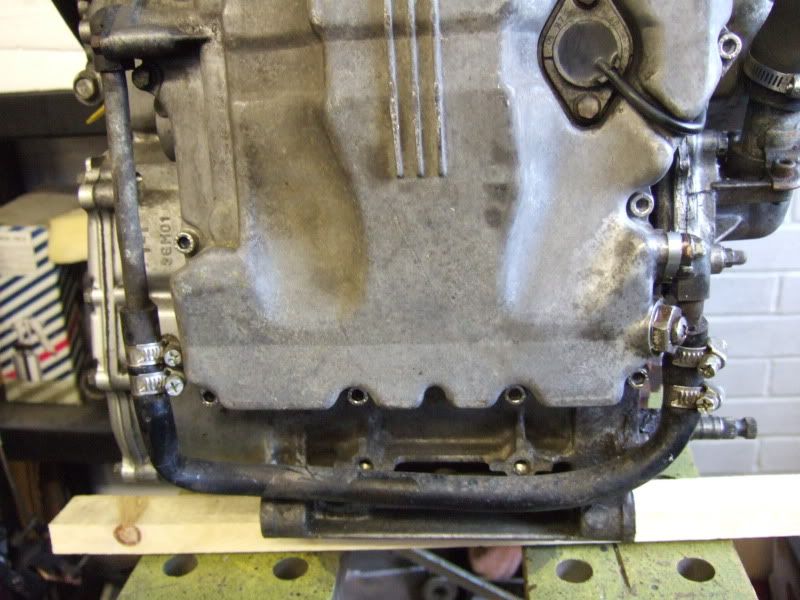
Now I'm all for inginuety and using what you have to hand, but this bolt takes the biscuit!!

took the sump off and cleaned out the pick up
Glad that mesh is in there.
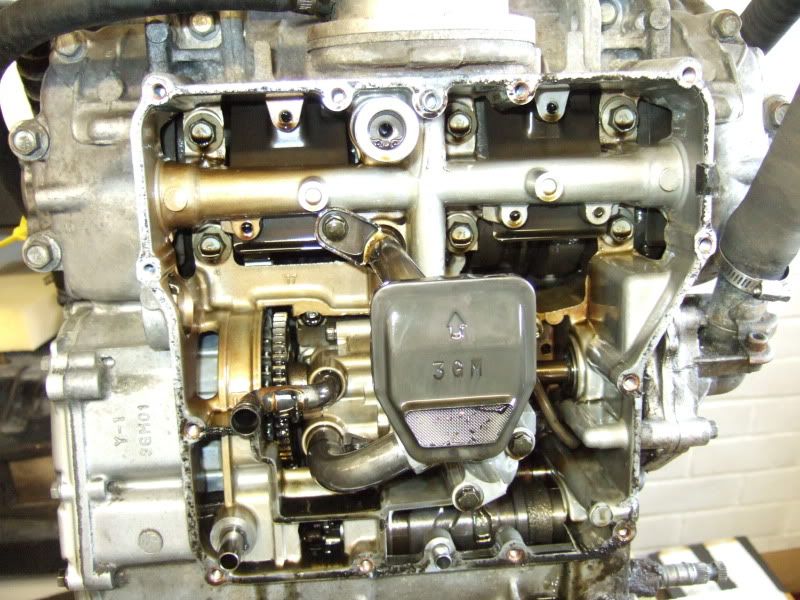
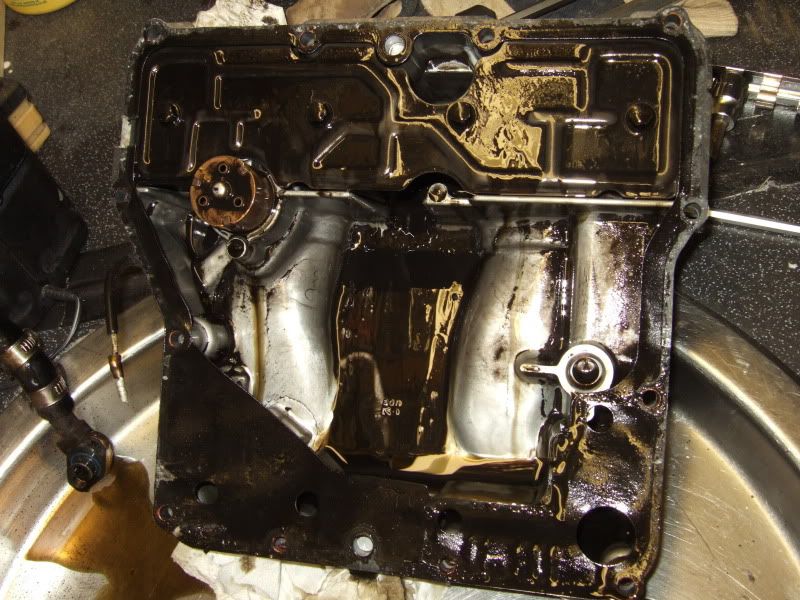
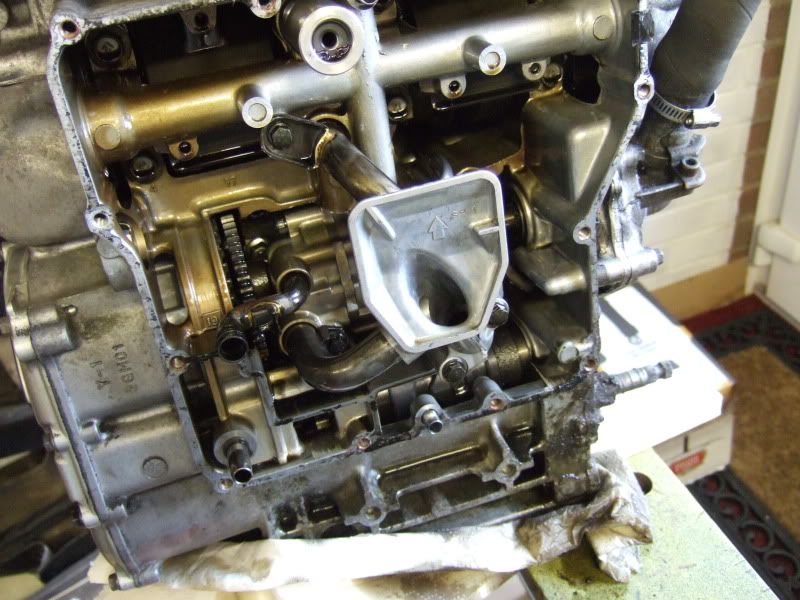
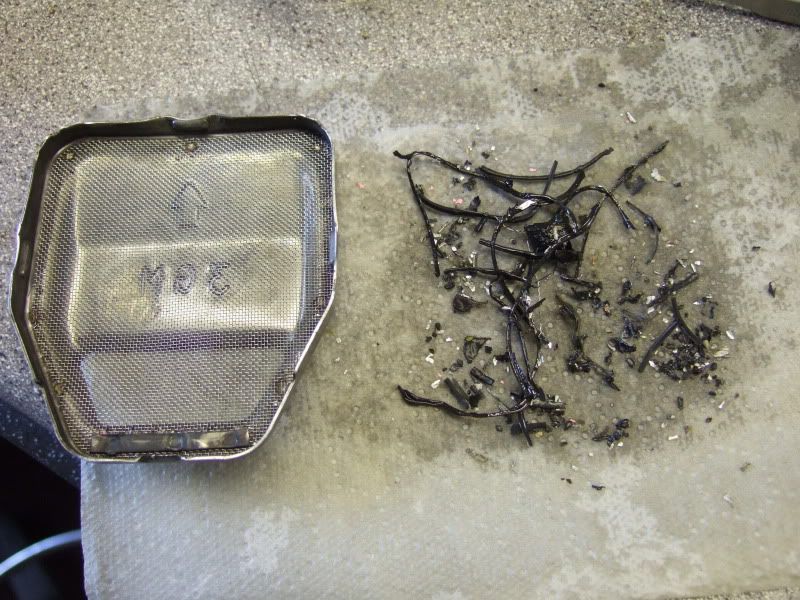
Then sat there for an hour with a scalpel cleaning the gasket off the engine case being VERY careful not to get any inside.
Regarding the cooler setup.
The two options I'm thinking about are these, use the existing cooler pipes, but re orientated so they point forwards, and join them to 10mm copper pipe that runs round the front of the engine, (brass 90 degree fitting just as an example) got to be better than the existing setup and relatively cheap to do.
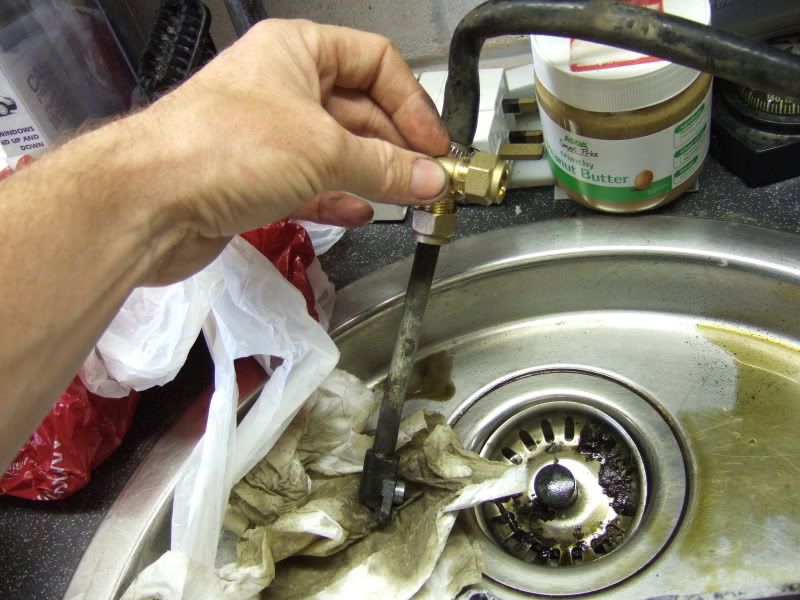
OR
tap the outlets on the sump to accept a banjo bolt and run a length of braided hose between the two.
My concerns with this are
1. the cost (money could be spent better elsewhere
)
2. Is there enough material around the outlets to allow tapping? anyone done this before?
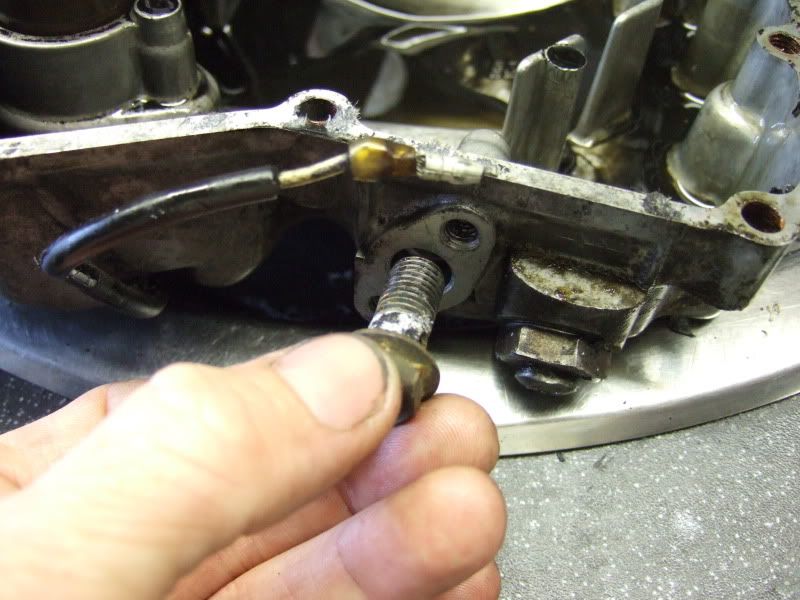
talking of money being better spent elsewhere, I noticed this the other day, a dink in the rear wheel.
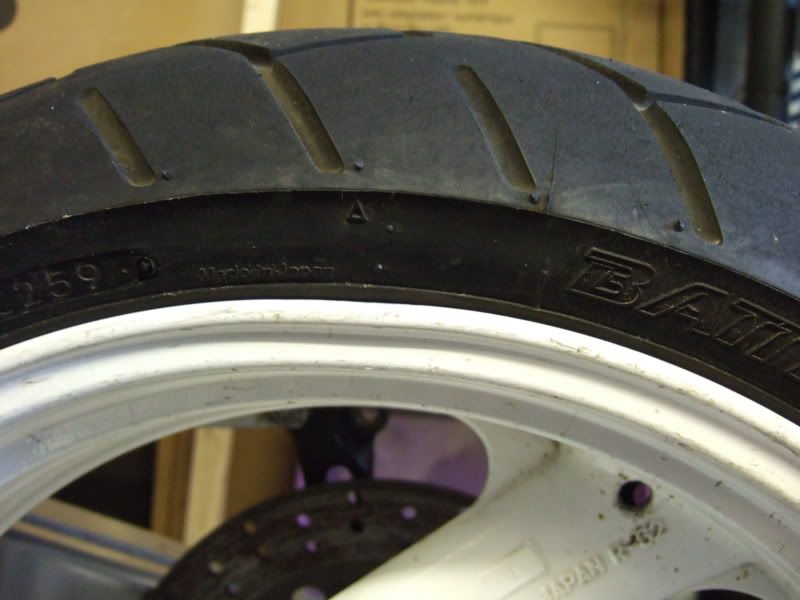
Oh and does anyone know the price of a sump gasket off the top of there heads
Rolled the engine onto its back so I could take the sump off and check all was well and to also try and figure out what to do about the oil cooler bypass arrangement.
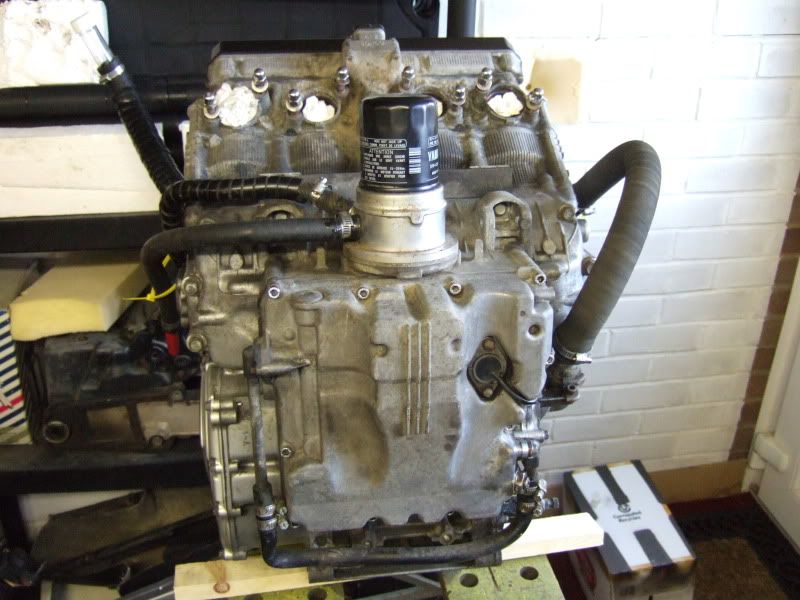
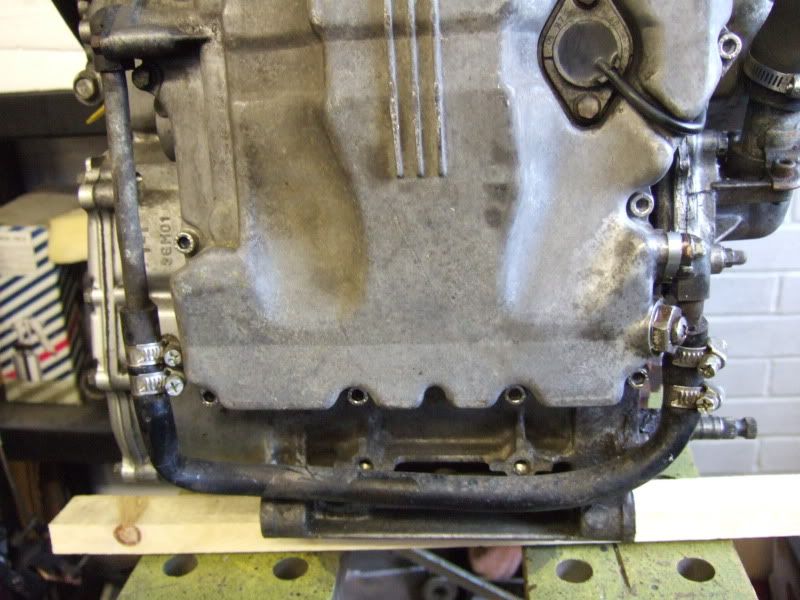
Now I'm all for inginuety and using what you have to hand, but this bolt takes the biscuit!!

took the sump off and cleaned out the pick up

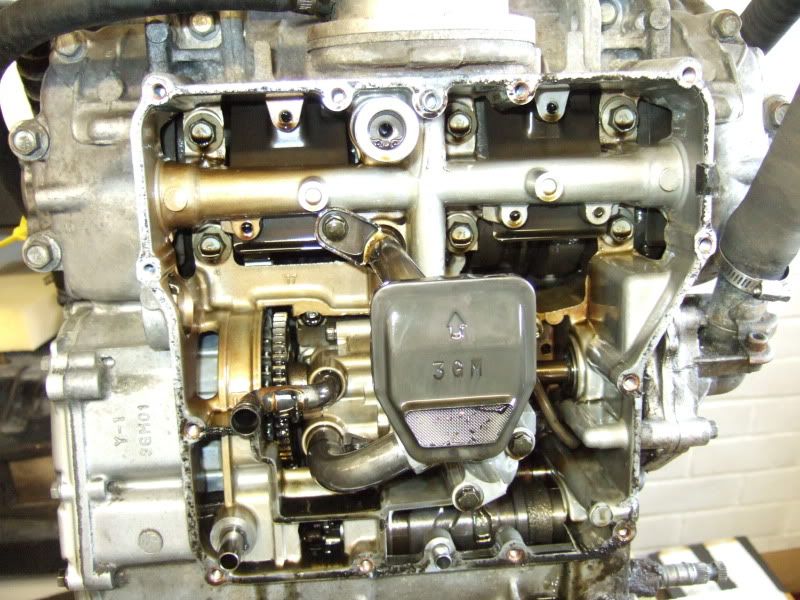
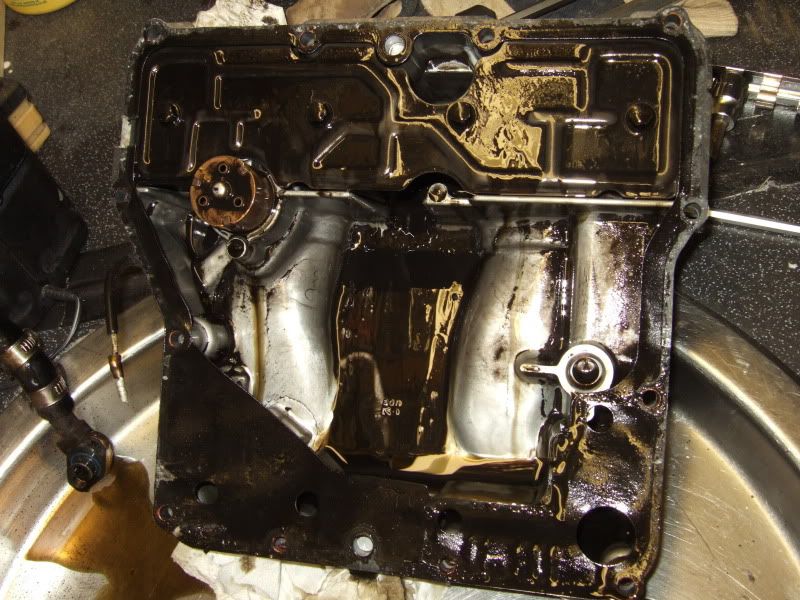
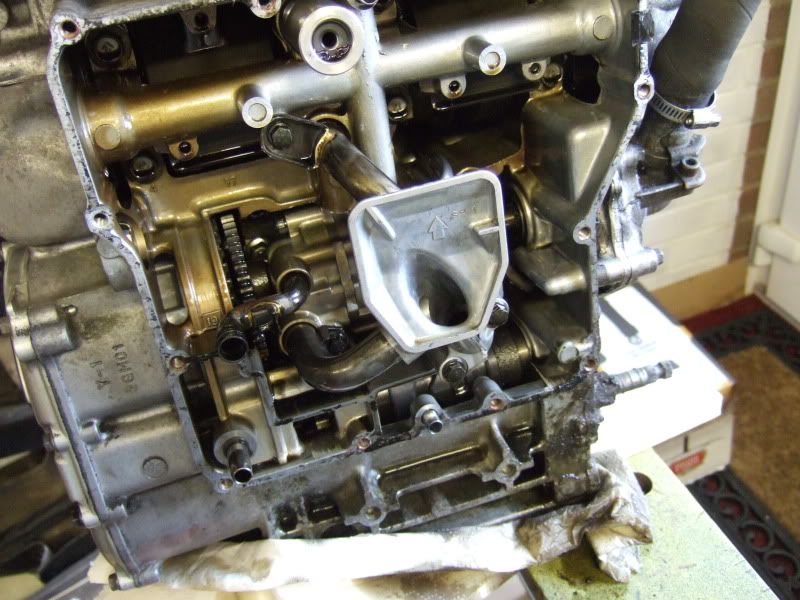
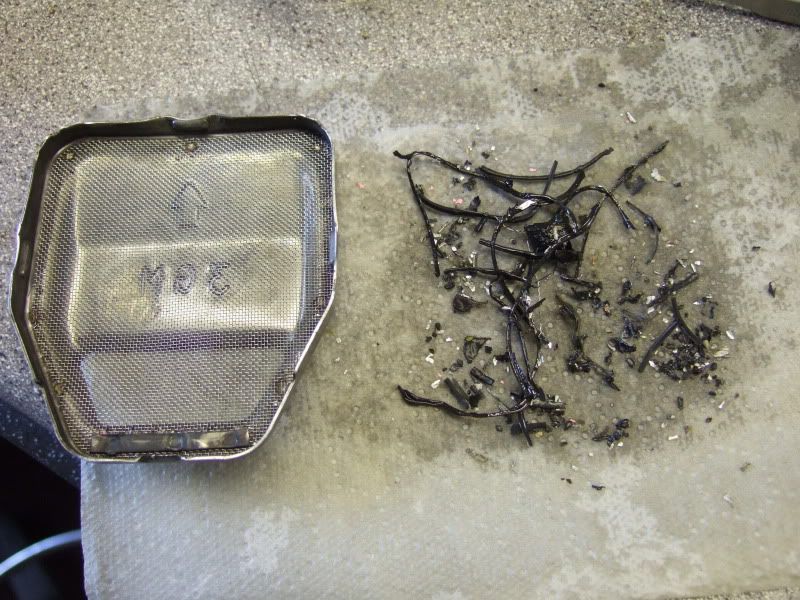
Then sat there for an hour with a scalpel cleaning the gasket off the engine case being VERY careful not to get any inside.
Regarding the cooler setup.
The two options I'm thinking about are these, use the existing cooler pipes, but re orientated so they point forwards, and join them to 10mm copper pipe that runs round the front of the engine, (brass 90 degree fitting just as an example) got to be better than the existing setup and relatively cheap to do.
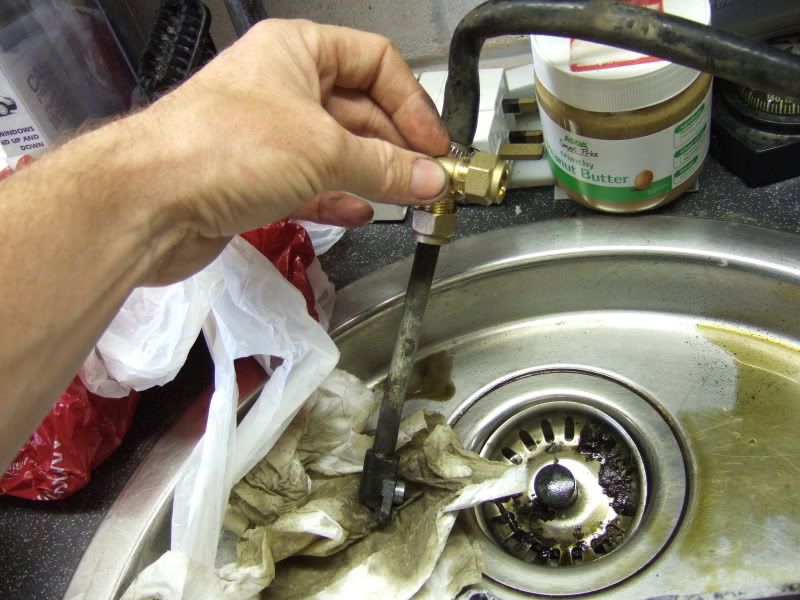
OR
tap the outlets on the sump to accept a banjo bolt and run a length of braided hose between the two.
My concerns with this are
1. the cost (money could be spent better elsewhere

2. Is there enough material around the outlets to allow tapping? anyone done this before?
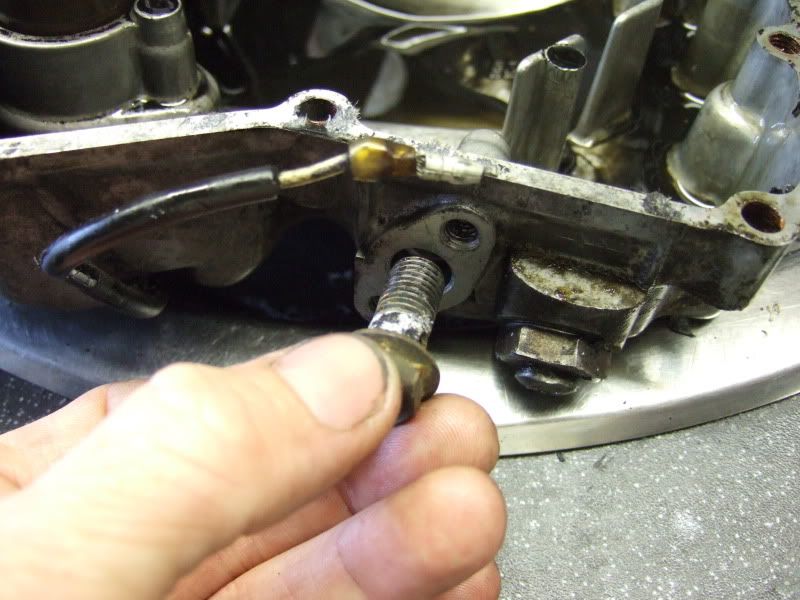
talking of money being better spent elsewhere, I noticed this the other day, a dink in the rear wheel.
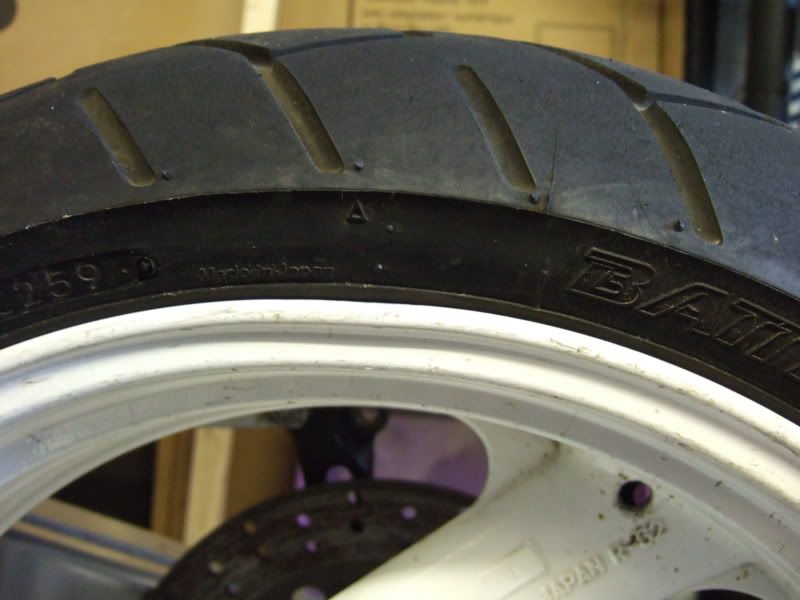
Oh and does anyone know the price of a sump gasket off the top of there heads

Never Ever Bloody Anything Ever!!!
So this afternoon I set about the task of replacing the oil cooler bypass line with something a little better than rubber hose.
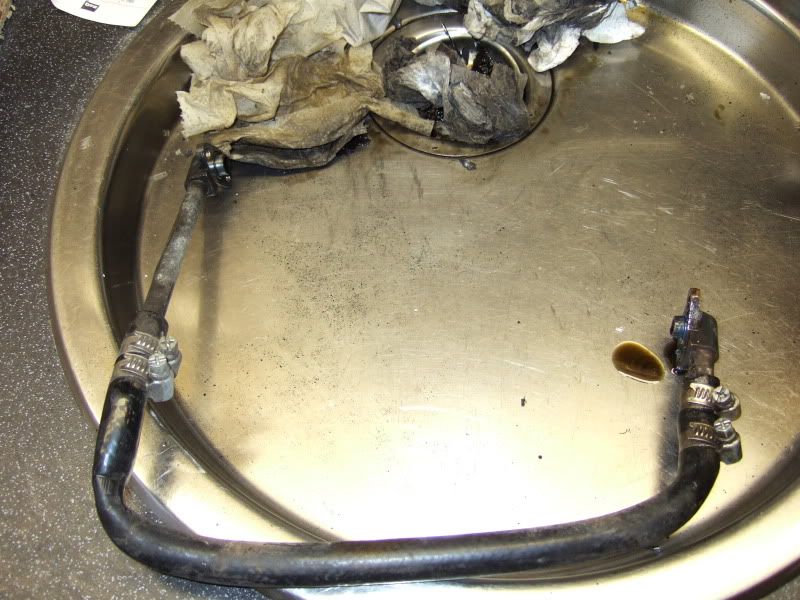
Once taken apart I could see what I had to play with.
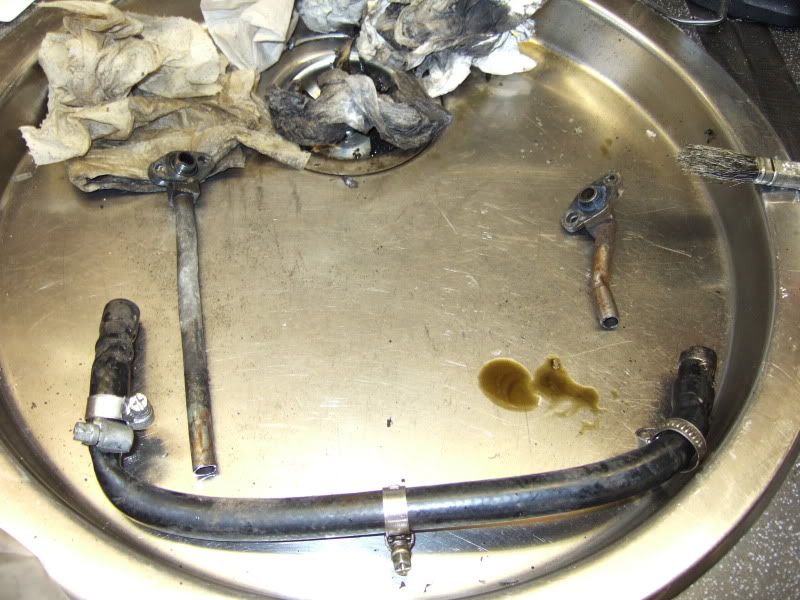
This is the route it took, I want to run it round the front of the engine to make access to the sump plug and refitting the engine easier. So I'll flip the fittings left to right and rotate through 180.
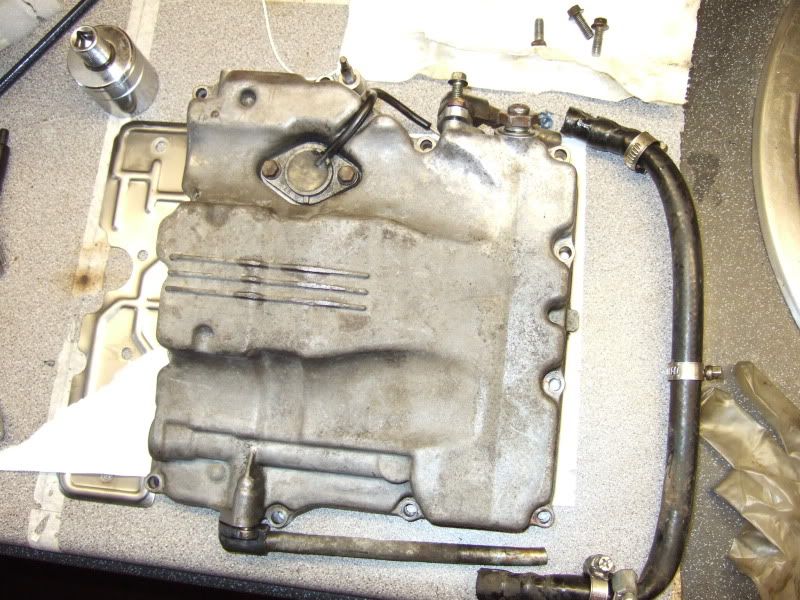
After a little tactical heating and bending I ended up with this
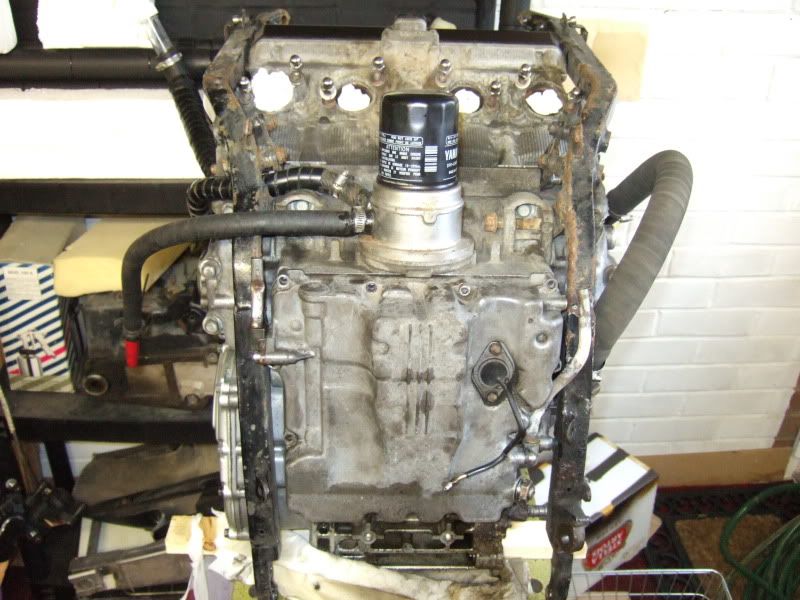
So before I got carried away I refitted the lower frame rails to make sure there was clearance
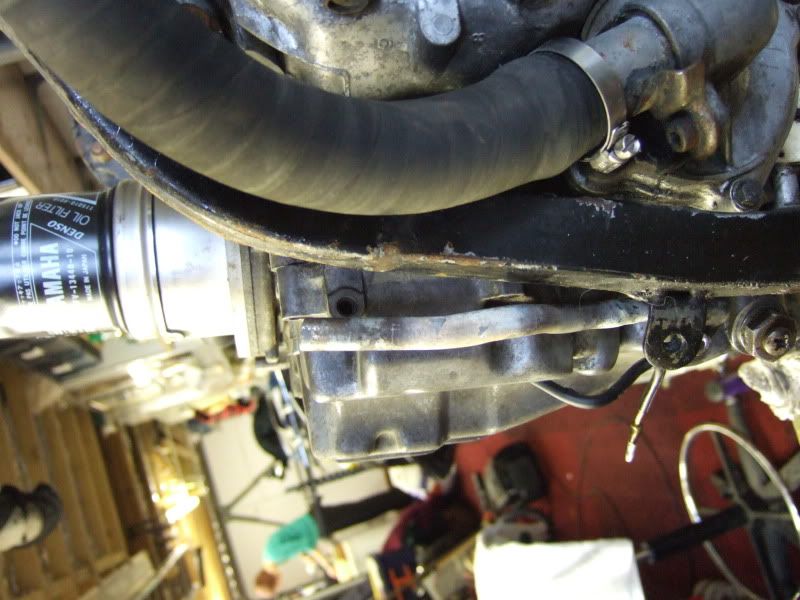
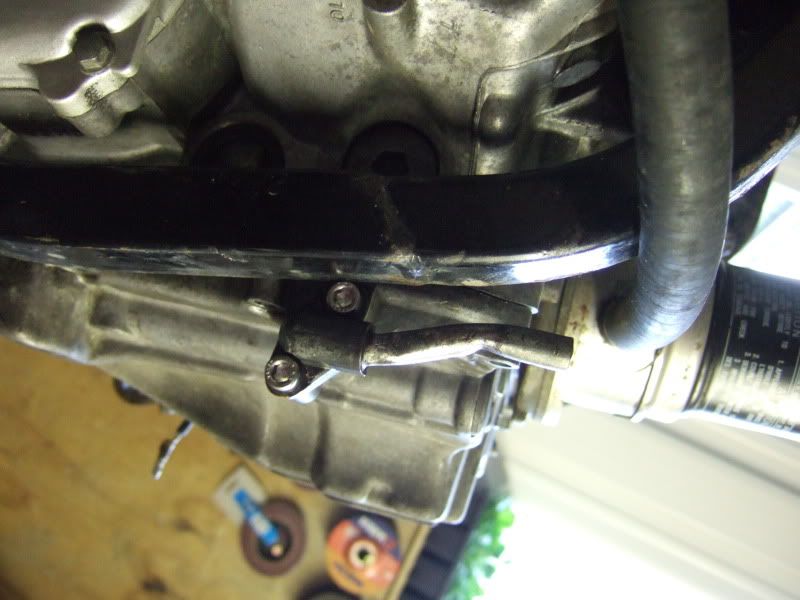
and this explains the crappy bolt!! clearance issues, so I'll replace allen head with a countersunk item.

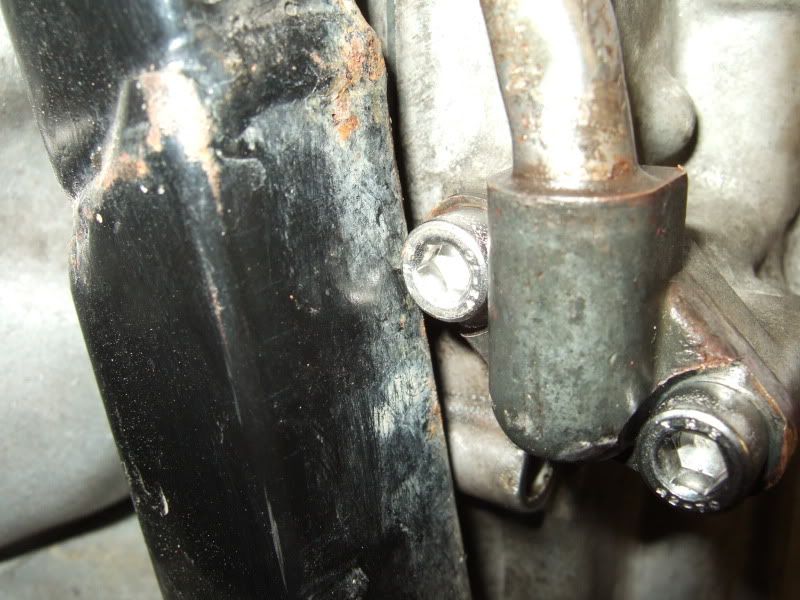
Decided to go the compression fitting route, may not look pretty but at least I won't have to worry about the hose splitting. and besides most of it will be hidden by the exhaust.
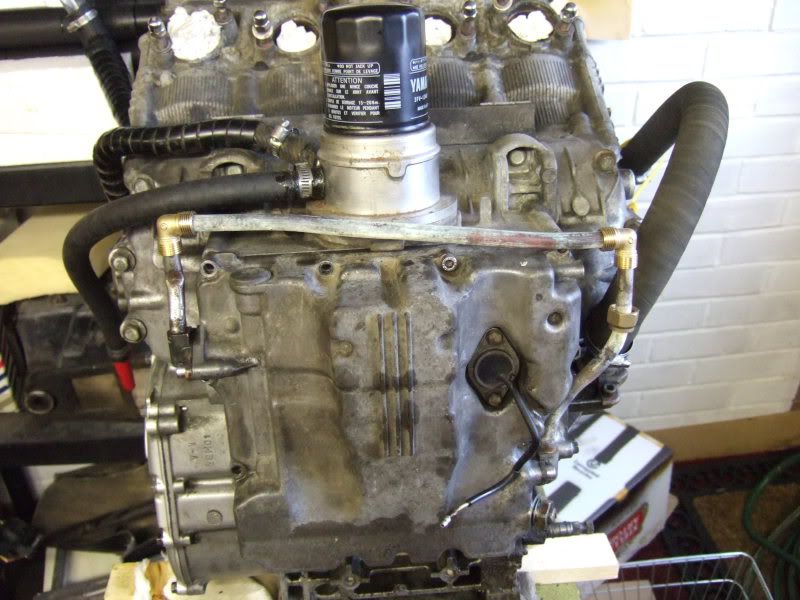
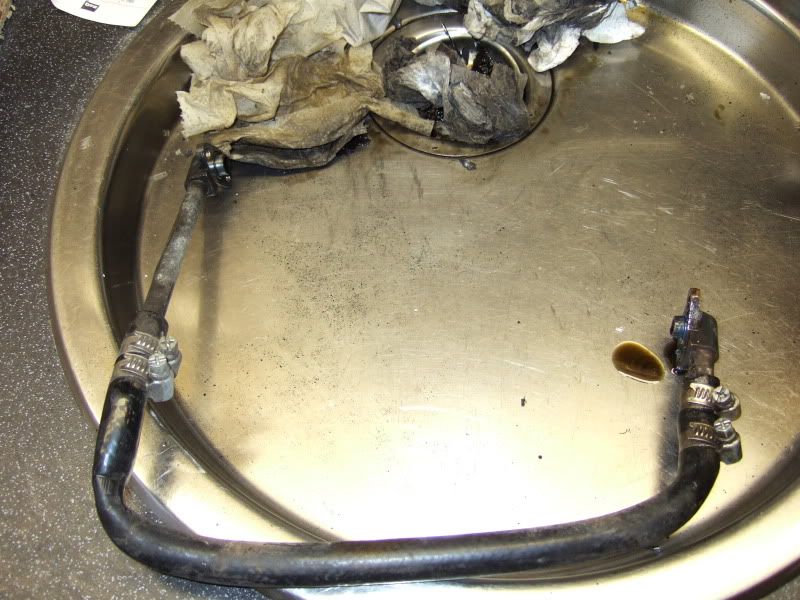
Once taken apart I could see what I had to play with.
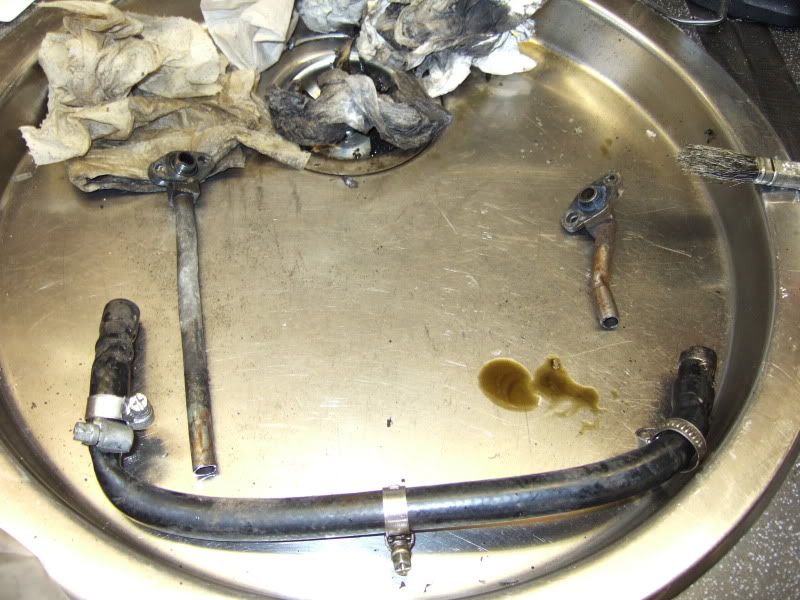
This is the route it took, I want to run it round the front of the engine to make access to the sump plug and refitting the engine easier. So I'll flip the fittings left to right and rotate through 180.
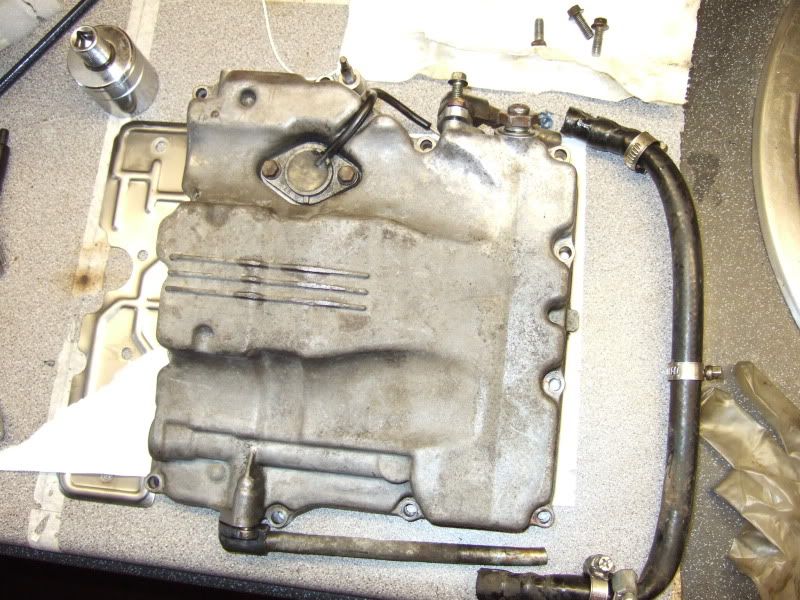
After a little tactical heating and bending I ended up with this
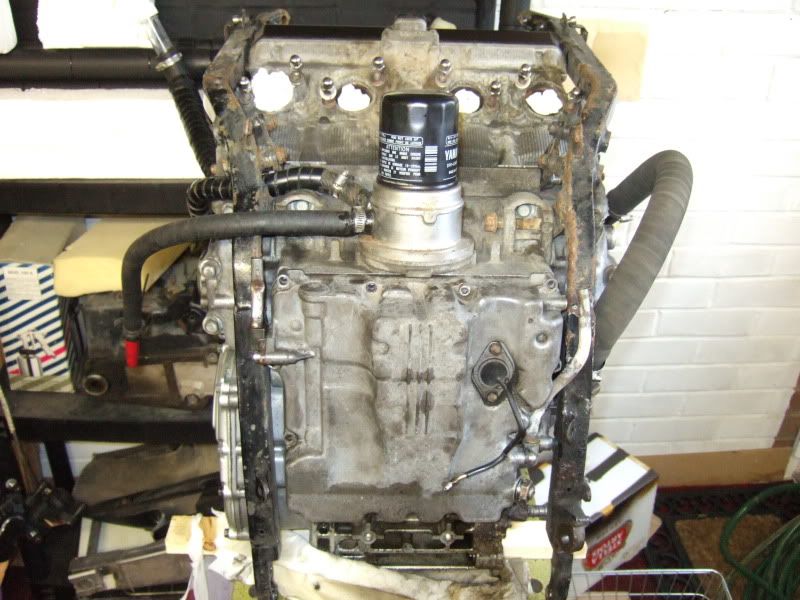
So before I got carried away I refitted the lower frame rails to make sure there was clearance
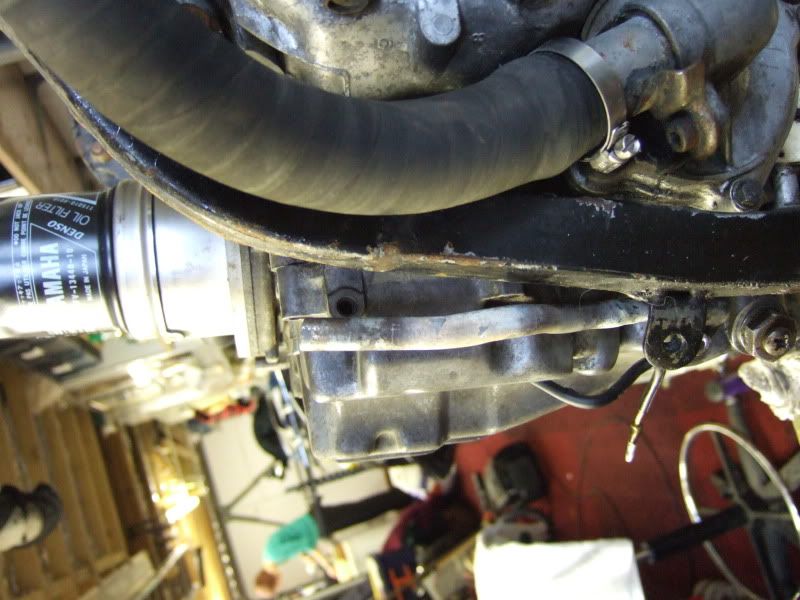
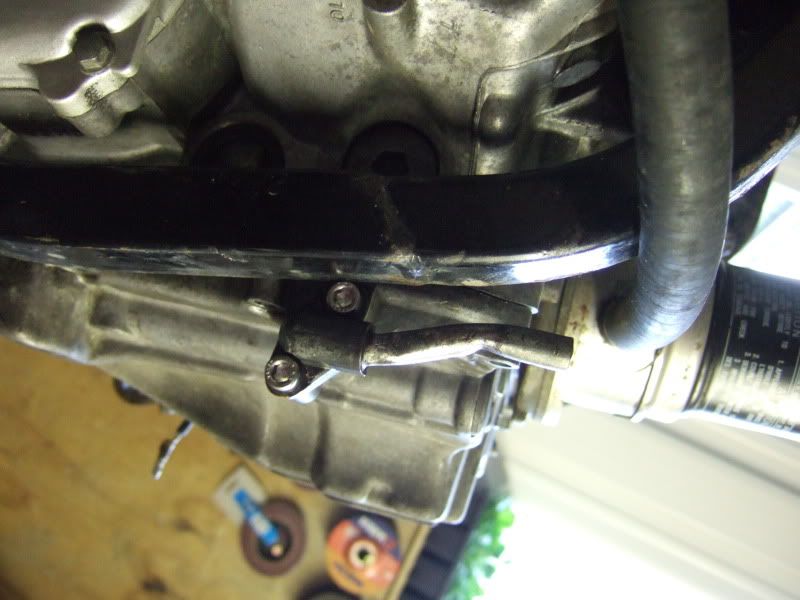
and this explains the crappy bolt!! clearance issues, so I'll replace allen head with a countersunk item.

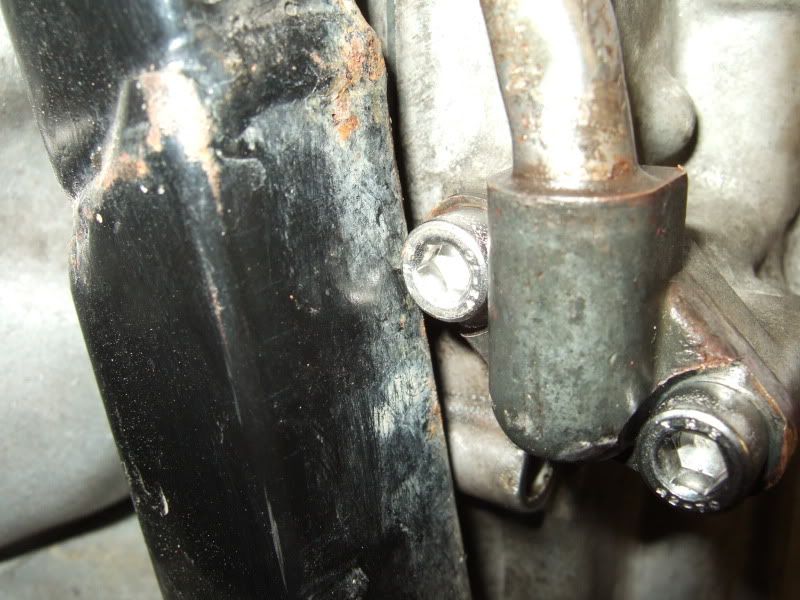
Decided to go the compression fitting route, may not look pretty but at least I won't have to worry about the hose splitting. and besides most of it will be hidden by the exhaust.
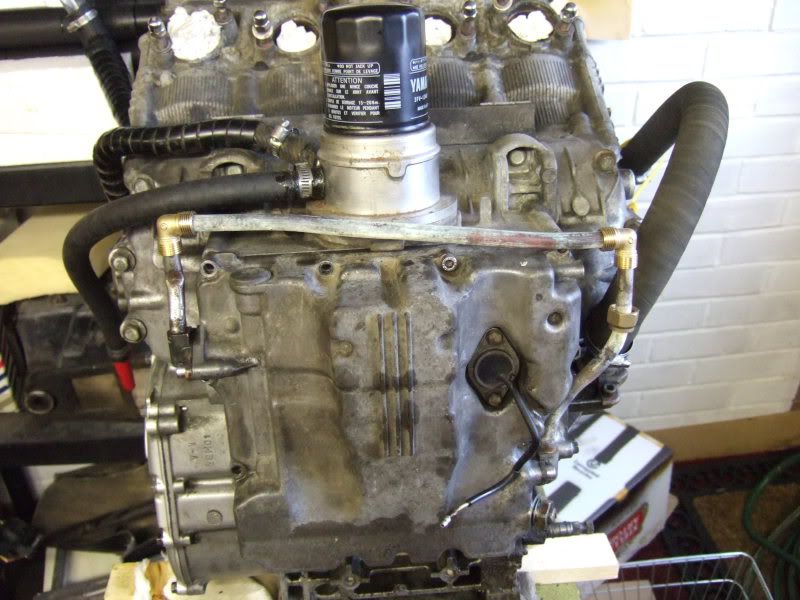
Never Ever Bloody Anything Ever!!!
Cheers guys,
spent a little more time today neatening up the right hand pipe, as it was too far away from the sump for my liking.
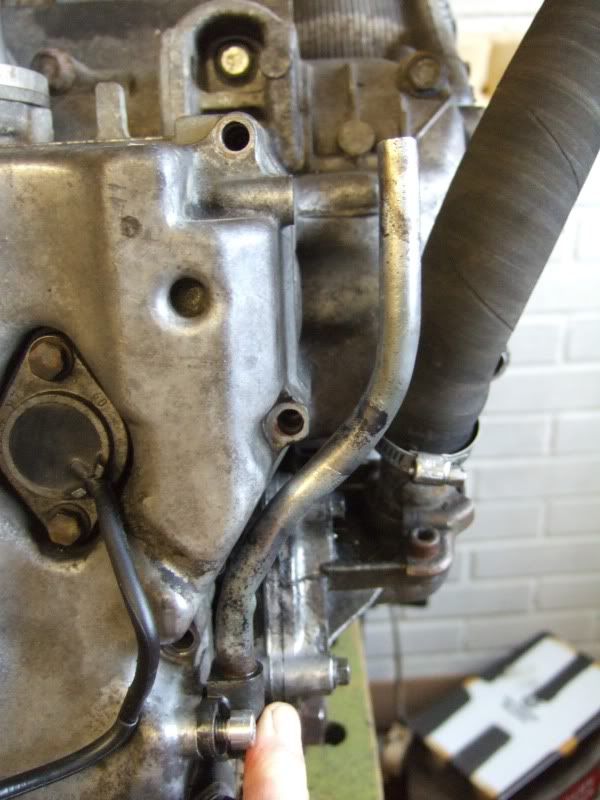
Managed to get a closer fit after ages spent heating and fetling. (this isn't the finished pipe as its touching the sump at the top, just forgot to take a pic)
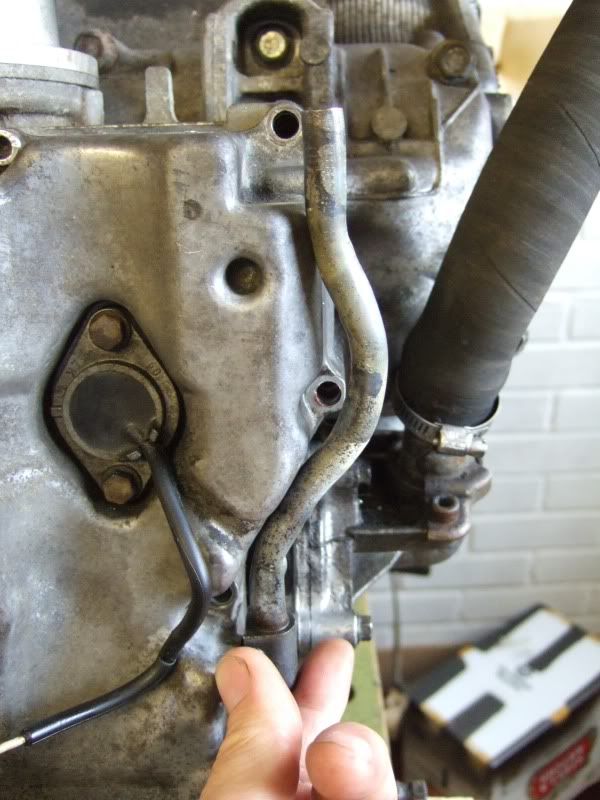
But I am not sure wether to go for compression fittings or solder joints, heres my reasoning.
When to original cooler pipes (steel) were cut they have been mishaped, although I have managed to get them back to a near circular state by using a 7.5mm drill shank inserted inside the pipe and tapping it with a hammer on the vice, see pics.
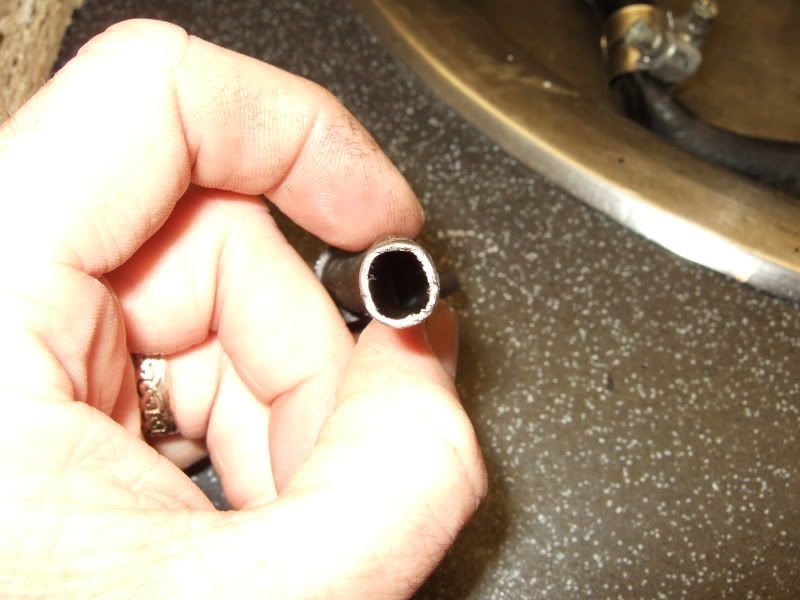
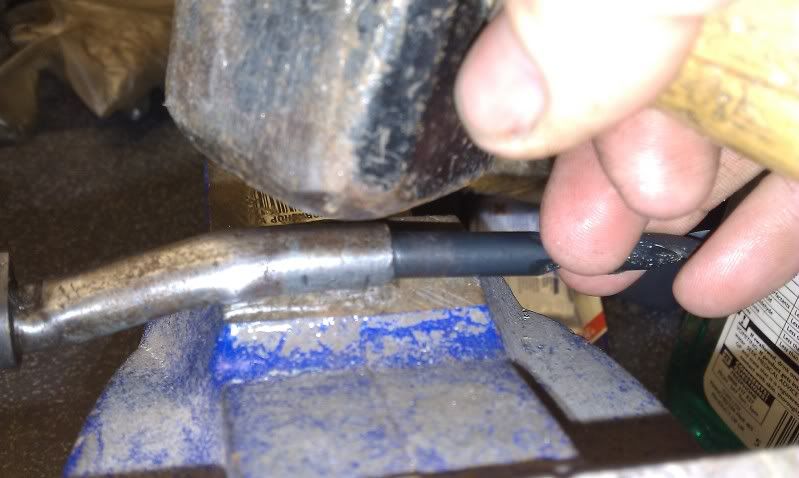
Now If I use solder elbows the thing will look less bulky, the solder should seal any gaps caused by the pipes slight mishape, and there shouldn't be an issue with temp as the solder melts at 180C ish whereas normal oil temp is 105C, Just the question of will the solder "take" on the steel pipe?
If I use compression fittings I can put instant gasket either side of the olive to help it seal, but it will look bulkier, will the olive compress and seal on the steel pipe, and if it does compress onto the steel pipe but still leaks there is not enough left to cut the olive off and go the solder route!
I have a couple of solder elbows coming in the post so I'll look at that option first.
In the meantime I painted the generator cover.
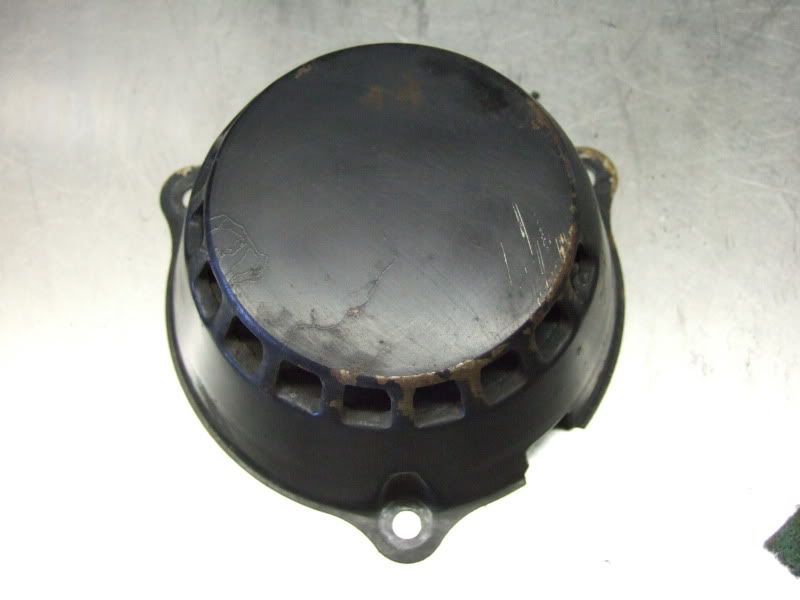
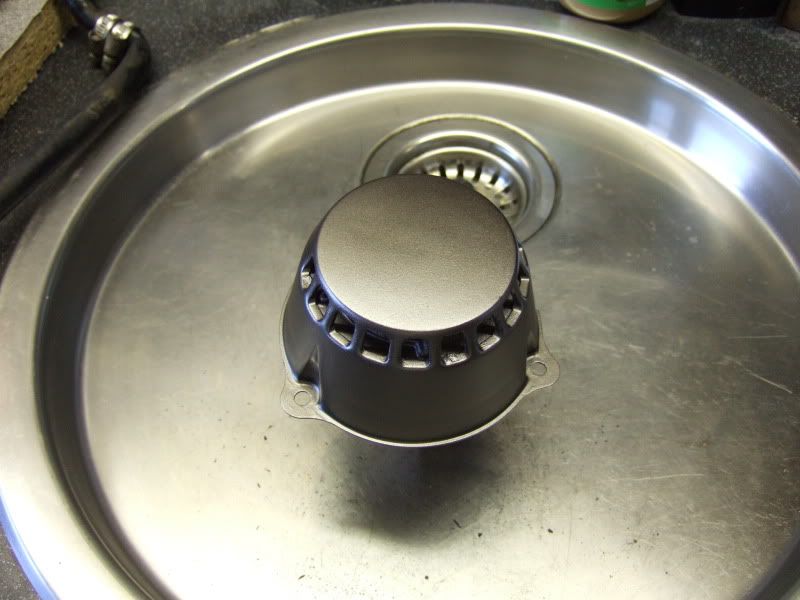
I also dug out a stainless bolt kit that I purchased whilst in the US 4 years ago, rather comprehensive and only $25 at the time.
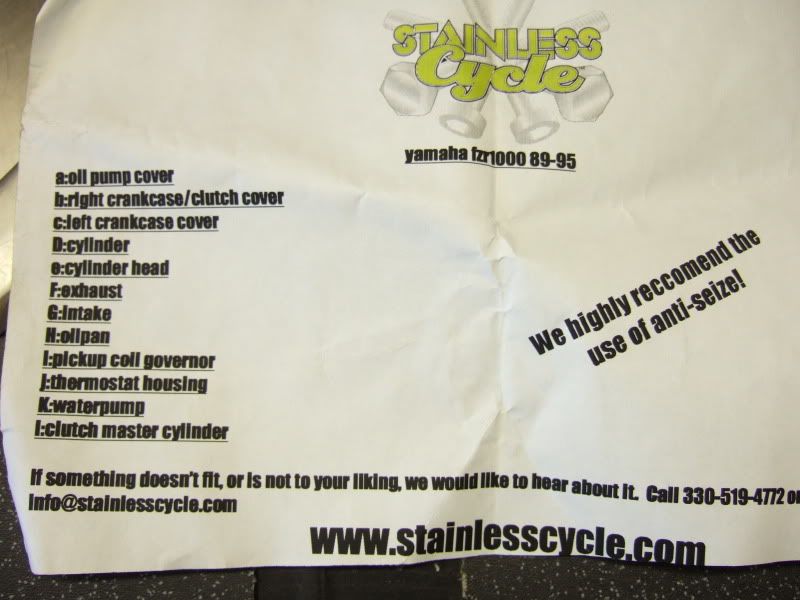
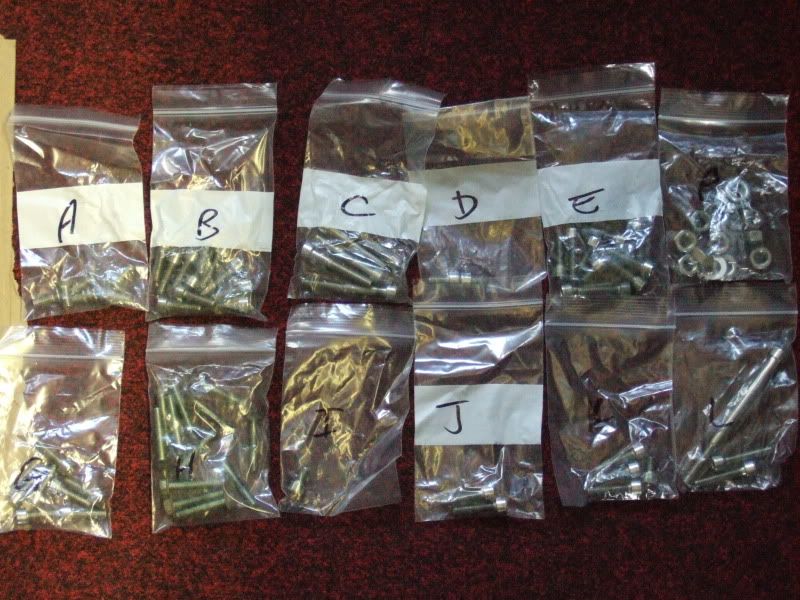
So will start fitting that to the engine while I am waiting for bits to arrive in the post.
Then hopefully I will be at the stage of getting the engine back in!!
spent a little more time today neatening up the right hand pipe, as it was too far away from the sump for my liking.
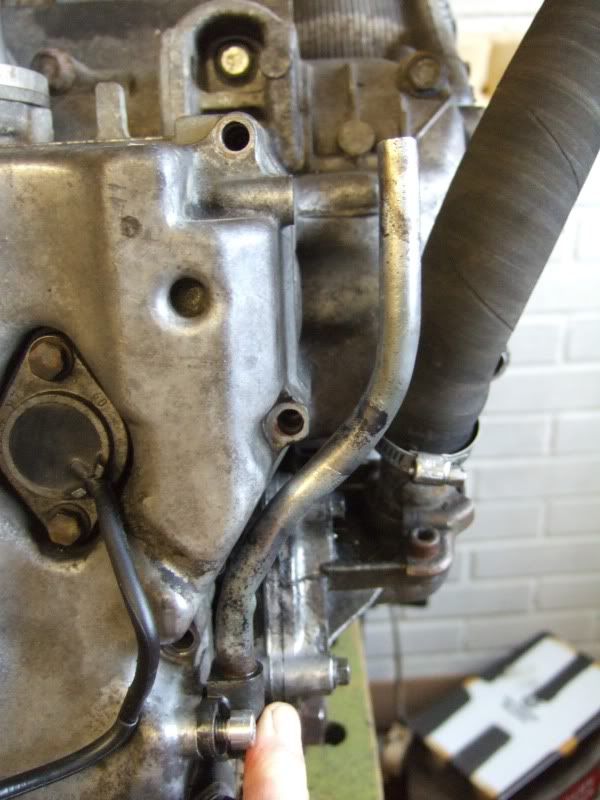
Managed to get a closer fit after ages spent heating and fetling. (this isn't the finished pipe as its touching the sump at the top, just forgot to take a pic)
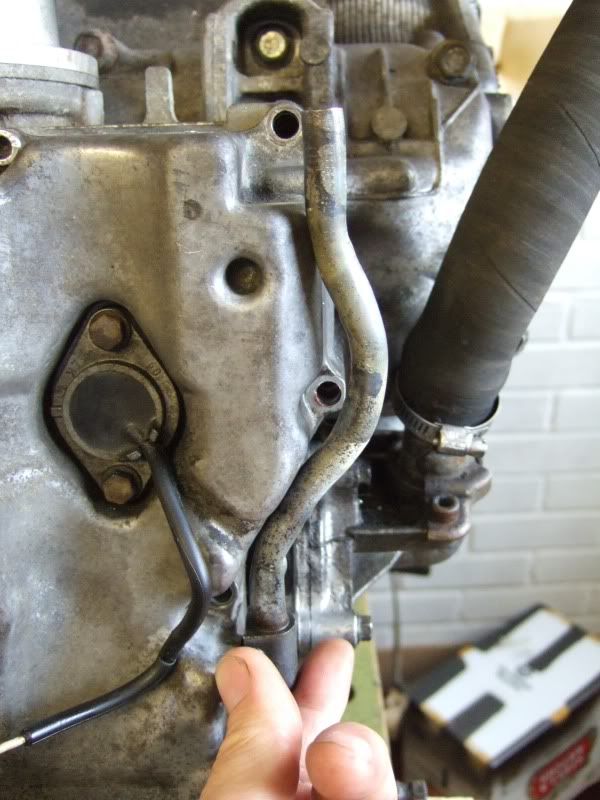
But I am not sure wether to go for compression fittings or solder joints, heres my reasoning.
When to original cooler pipes (steel) were cut they have been mishaped, although I have managed to get them back to a near circular state by using a 7.5mm drill shank inserted inside the pipe and tapping it with a hammer on the vice, see pics.
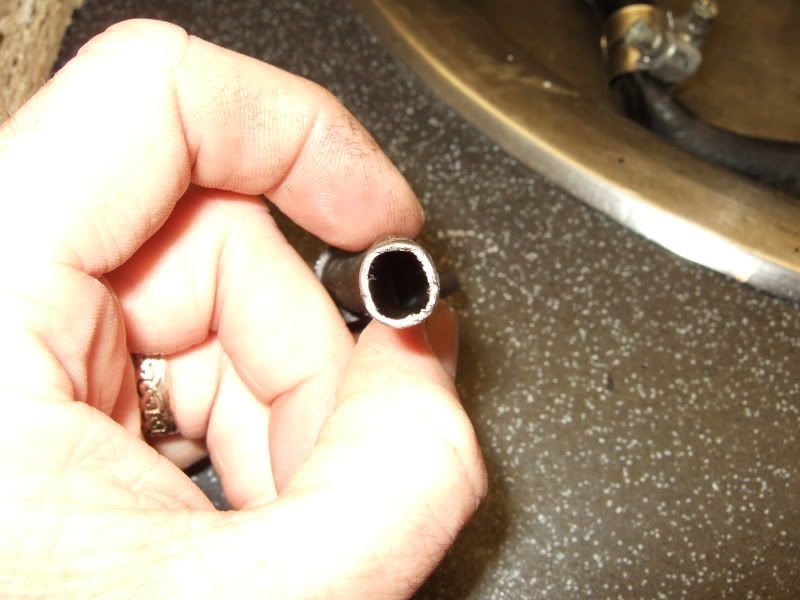
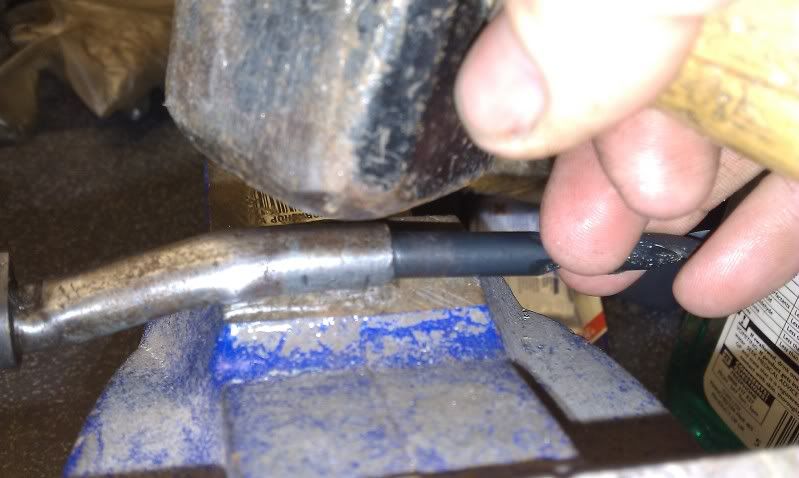
Now If I use solder elbows the thing will look less bulky, the solder should seal any gaps caused by the pipes slight mishape, and there shouldn't be an issue with temp as the solder melts at 180C ish whereas normal oil temp is 105C, Just the question of will the solder "take" on the steel pipe?
If I use compression fittings I can put instant gasket either side of the olive to help it seal, but it will look bulkier, will the olive compress and seal on the steel pipe, and if it does compress onto the steel pipe but still leaks there is not enough left to cut the olive off and go the solder route!
I have a couple of solder elbows coming in the post so I'll look at that option first.
In the meantime I painted the generator cover.
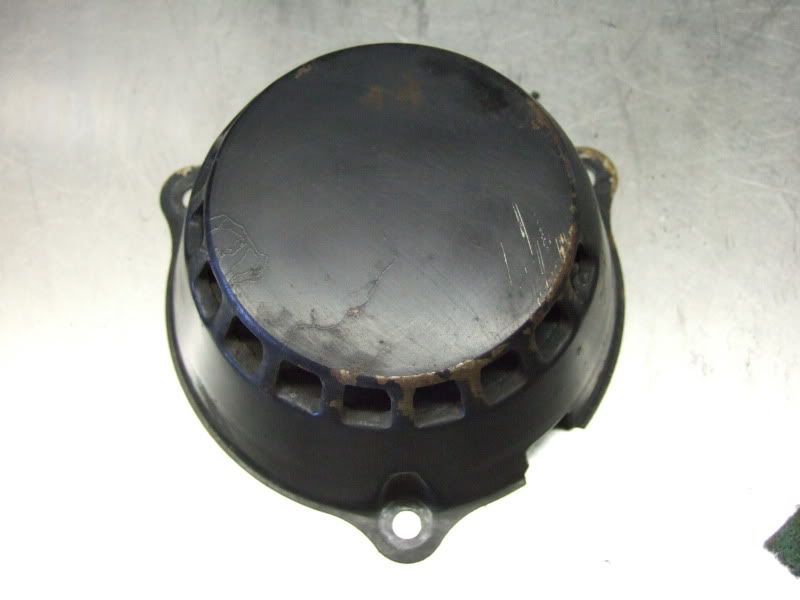
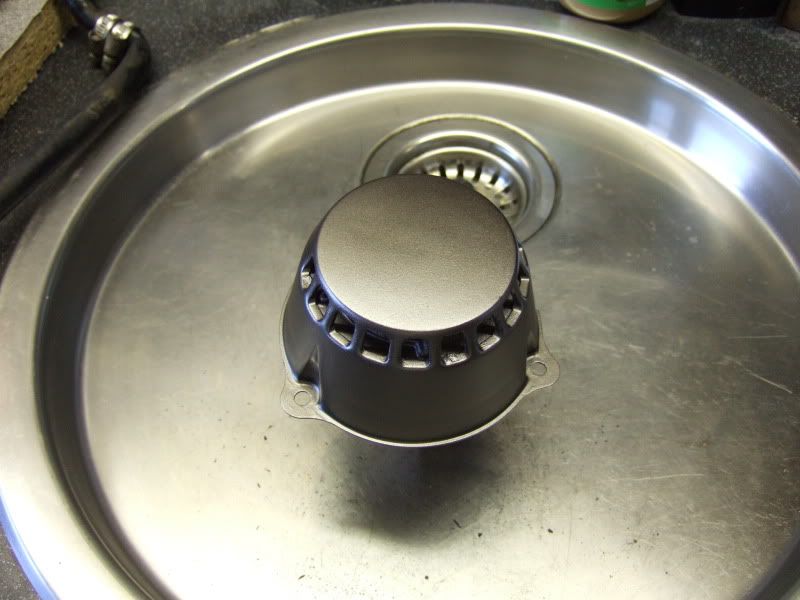
I also dug out a stainless bolt kit that I purchased whilst in the US 4 years ago, rather comprehensive and only $25 at the time.
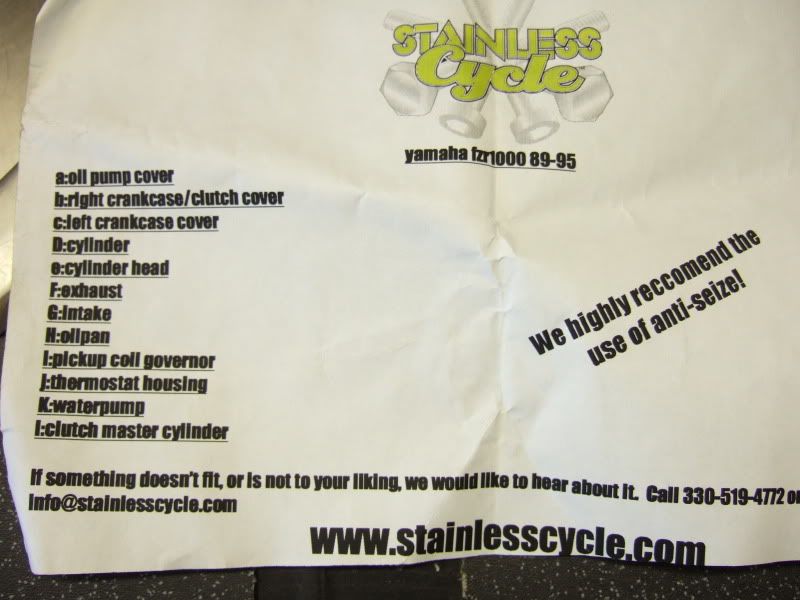
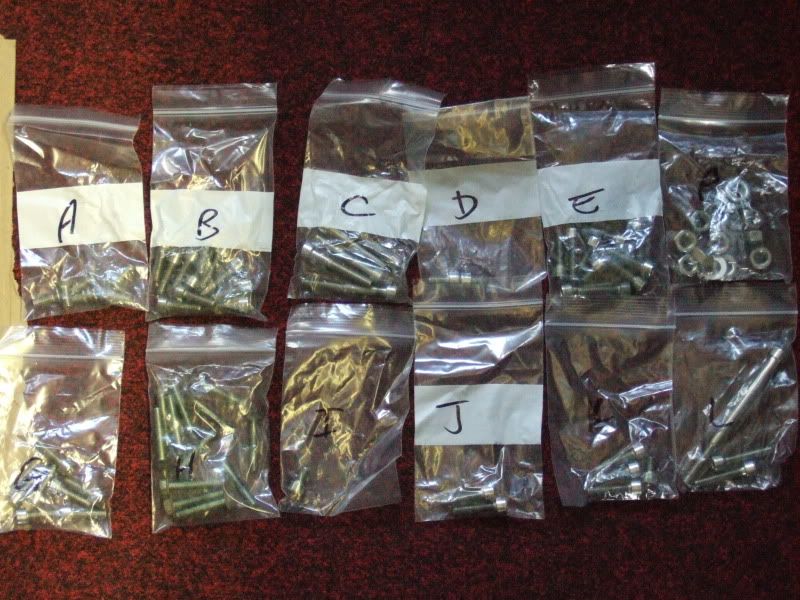
So will start fitting that to the engine while I am waiting for bits to arrive in the post.
Then hopefully I will be at the stage of getting the engine back in!!

Never Ever Bloody Anything Ever!!!
Here you go fang. It'll save your name going in stigs black book
It's easy even I can do it.
Shortening links


It's easy even I can do it.

Shortening links
Bit of advice. Buy a good bed and a good pair of shoes, because if you aren't in one you'll be in the other.
Little Black Booknuggitt wrote:Here you go fang. It'll save your name going in stigs black book![]()
![]()
It's easy even I can do it.![]()
Shortening links


Pornography
Oh yeah, So it is, cheers Nuggitt and

Never Ever Bloody Anything Ever!!!
Who is online
Users browsing this forum: Amazon [Bot] and 0 guests